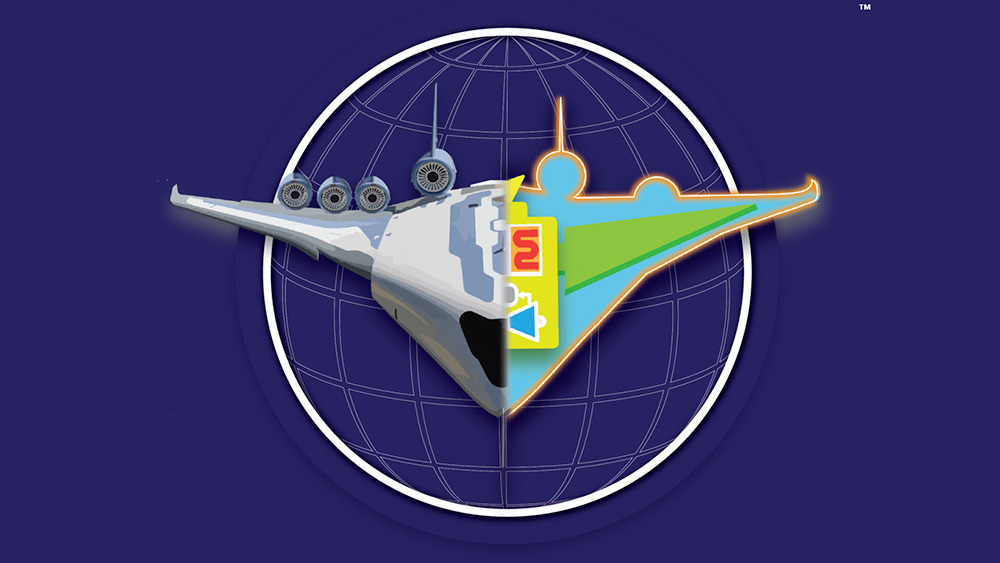
Researchers at Texas A&M University are working to develop an all-electric propulsion system for single-aisle, 150-200 passenger commercial aircraft, such as the Boeing 737, that will significantly decrease the amount of greenhouse gas emissions affecting the environment through commercial air travel.
It is estimated that single-aisle aircraft are responsible for nearly half of aviation-related greenhouse gas emissions. In 2017, domestic air travel consumed nearly 3.5 quadrillion British thermal units of jet fuel, accounting for about 3.5% of primary energy consumption and about 2.6% of greenhouse gas emissions in the United States.
Dr. Hamid Toliyat, Raytheon Professor in the Department of Electrical and Computer Engineering, received funding to continue with phase two of the $5 million U.S. Department of Energy’s Advanced Research Projects Agency-Energy (ARPA-E) Aviation-class Synergistically Cooled Electric-motors with iNtegrated Drives (ASCEND) project. The program aims to address the greenhouse gas issue by creating innovative, lightweight and ultra-efficient electric motors, drives and associated thermal management systems (collectively referred to as the all-electric powertrain).
By using carbon-neutral liquid fuels, such as ethanol or green ammonia, an all-electric propulsion system would have net-zero emissions and be much quieter for passengers and those in the vicinity of airports.
The goal with the completion of the second and final phase of the ASCEND program is a fully integrated all-electric powertrain system at a power density of 12 kilowatts per kilogram or greater with an efficiency of 93% or greater. These targets are beyond the capability of current advanced technologies, but Toliyat and his team are working to push the boundaries to make this achievement possible.
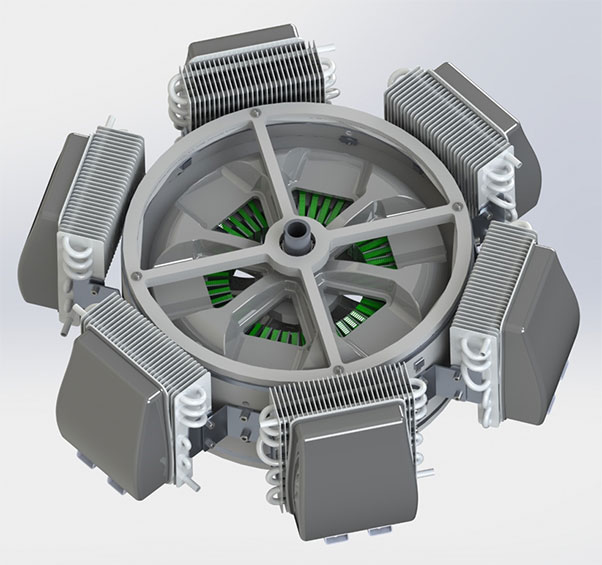
During phase one of the project, the design and model were developed. During phase two, the development and implementation stages will begin.
“During phase one, we were able to show that the full power train is manufacturable by using cutting-edge technology, including 3D printing and metal additive manufacturing,” said Dorsa Talebi, a doctoral student working with Toliyat.
The project is funded by ARPA-E through the Texas A&M Engineering Experiment Station. Led by Toliyat, this project includes many collaborators across the College of Engineering, including nine faculty and their respective graduate and doctoral students from the Department of Electrical and Computer Engineering, the Department of Aerospace Engineering, the Department of Materials Science and Engineering and the J. Mike Walker ’66 Department of Mechanical Engineering. Dr. Matthew Gardner, assistant professor at The University of Texas at Dallas and former doctoral student of Toliyat’s, is serving as co-principal investigator for this project. Texas A&M Technology Commercialization, which is an office on campus connecting industry to The Texas A&M University System, is also involved with the project.