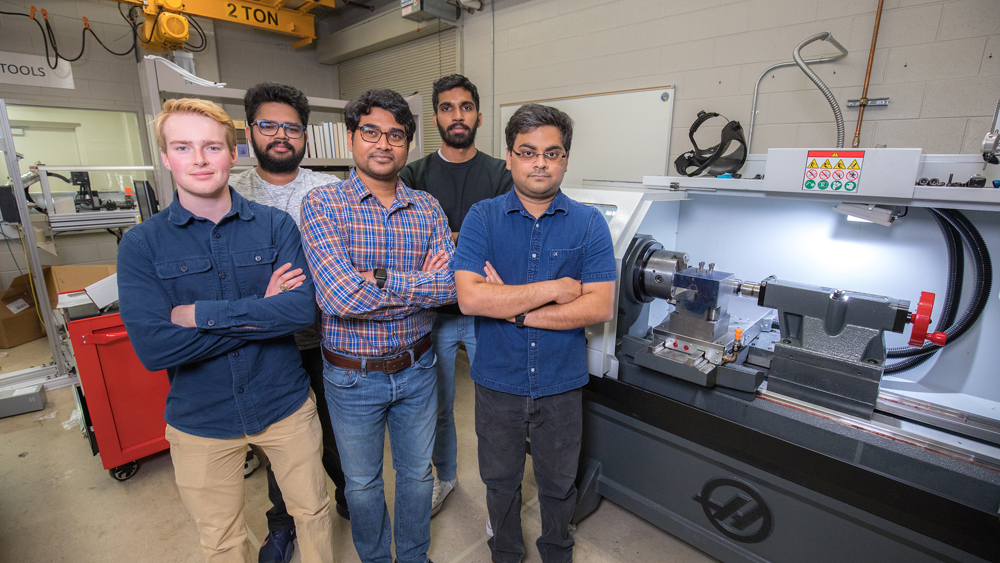
Dr. Dinakar Sagapuram, assistant professor in the Wm Michael Barnes ‘64 Department of Industrial and Systems Engineering at Texas A&M University, has been named a 2021 Breakthrough Energy Fellow for his work on clean energy manufacturing technologies. Sagapuram will lead the research with his colleague and co-investigator Dr. Prabhakar Pagilla, professor in the J. Mike Walker ’66 Department of Mechanical Engineering and associate dean for research in the Texas A&M College of Engineering, to develop their new strip steel manufacturing technology called MetPeel to reduce emissions in one of the hardest sectors to decarbonize — steel.
Founded by Bill Gates, Breakthrough Energy (BE) is committed to supporting the development and adoption of breakthrough clean technologies the world needs to reach net-zero emissions by 2050. BE Fellows is their latest program specifically designed to provide researchers with funding, mentorship, education and access to the BE network with the aim to accelerate new technologies from early development to widespread deployment.
The 2021 inaugural BE Fellows cohort consists of researchers from leading research institutions in North America, Europe and New Zealand, working in steel, cement, hydrogen, fertilizer and electrofuels. The projects and fellows were selected through an extremely competitive application process from across the globe. Sagapuram is one of the only 17 fellows selected this year and the only one working in steel.
The iron and steel sector is the largest industrial emitter of carbon dioxide — the primary driver of climate change. According to the World Steel Association, almost two tons of carbon dioxide are emitted for every ton of steel produced, making the steel industry responsible for about 4 billion tons of greenhouse gas emissions every year — or 8% of all global greenhouse gas emissions.
The significant amount of energy needed to convert raw iron ore into final useful steel is the reason why steel manufacturing is so carbon-intensive. For example, the principal route to shape cast steel ingots into final products is rolling — a complex multistep process where large thickness reductions are achieved in small increments through several hot and cold rolling steps. This process requires repeated high-temperature heating (as in thousands of degrees Fahrenheit) and cooling of the material as it passes through multiple rollers, and nearly 85% of the energy is obtained by burning fossil fuels, which results in direct carbon emissions.
The researchers, who are part of the Texas A&M Engineering Experiment Station (TEES), created technology that reimagines how a steel strip is manufactured. MetPeel disrupts the traditional rolling-based manufacturing processes by producing steel strips through a more efficient, single-step process. The process involves machining a thin, continuous metal strip from the circumference of a rotating feedstock using a sharp cutting tool, similar to how wood veneer is produced.
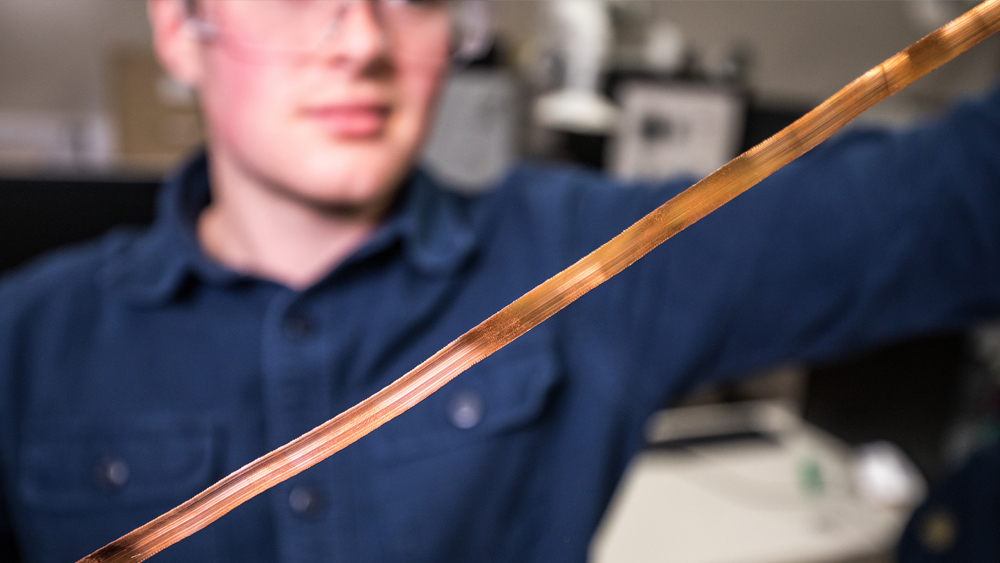
The primary advantage of MetPeel is that the shape change from bulk material to thin strip is accomplished in just one deformation step. This lowers energy usage significantly. Moreover, the process reduces the need for external heating and therefore could be operated using electricity alone, which eliminates the need for fossil fuels. This one-step process for transforming raw material into a final strip product is clean and significantly more efficient than the current greenhouse gas-emitting technologies.
“I’m honored to be selected as a BE Fellow and to be joining this impressive cohort,” said Sagapuram, who joined Texas A&M in 2016 following his Ph.D. and postdoctoral work at Purdue.
Currently, most of the decarbonization efforts in steel focus primarily on ironmaking and steelmaking processes, where different clean sources like hydrogen, electricity and biomass are being explored as alternative reductants or fuel in place of coal. But the practice of shaping cast steel into a thin sheet via multiple deformation steps using rolling has not changed all that much over the last 100 years, although rolling is known to be one of the most energy-intensive processes.
“MetPeel disrupts this paradigm by enabling strip production in far fewer steps and within a compact physical footprint,” said Sagapuram. “This directly translates to energy efficiency and lower cost. The benefits are tremendous, especially for thinner strips. This is because, in contrast to rolling where specific energy (energy per unit kg) and cost increase exponentially as the strip gets thinner, energy consumption in our process is independent of thickness.”
The built-in advantage of being less expensive than conventional technology sets MetPeel apart from other clean energy technologies.
“Most current clean technology solutions that can replace existing high-emission technologies incur an additional cost — the Green Premium,” said Pagilla. “MetPeel eliminates the Green Premium for steel. It is not only a clean technology alternative to steel strip rolling, but it also costs less, which essentially means it has a ‘negative’ Green Premium.”
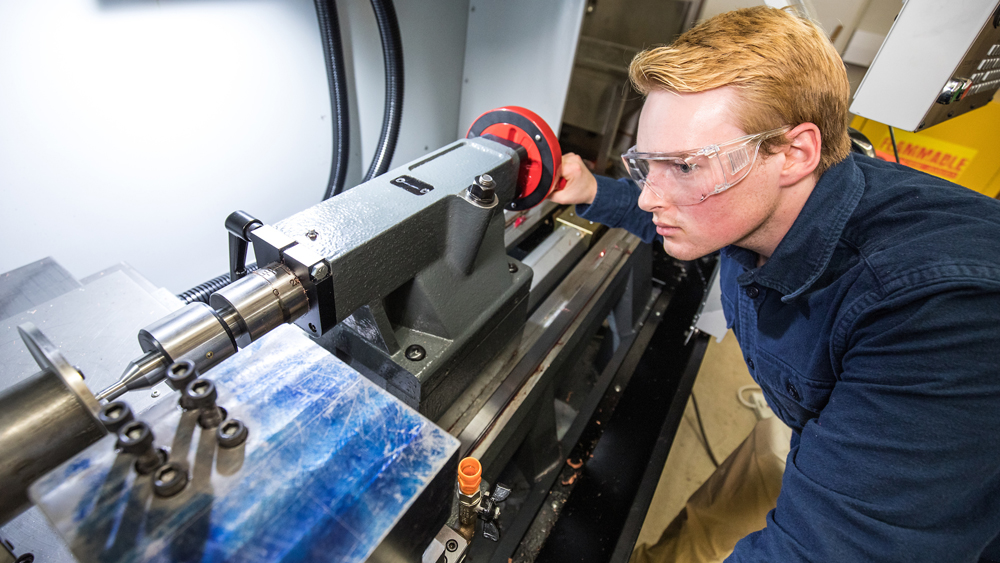
The team’s research at the lab-scale has revealed yet another attractive feature of the process — the ability to precisely control the internal grain structure of the sheet, which is typically difficult to achieve using rolling. Therefore, the strip can even be made with superior quality and mechanical properties compared to conventional rolled steel.
“Although the technology can be applied to manufacture virtually any metal with better properties and at lower energy, steel is our initial target because of its widespread use and significant potential for impact,” Sagapuram said.
“The Breakthrough Energy Fellows program identifies and supports the best and brightest individuals and teams across the globe working to develop, scale and commercialize technologies that have the potential to reduce carbon emissions by at least 500 million tons per year by 2050,” said Ashley Grosh, vice president of Breakthrough Energy Fellows. “We’re thrilled to support MetPeel’s critical work to decarbonize steel production and help reimagine our sustainable future.”
As part of the BE Fellows program, the team will work toward process scaling and developing control tools needed for widespread adoption while quantifying the emissions and energy-reduction potential of the technology.
“The Breakthrough Energy Fellows program is attractive and unique,” Pagilla said. “It not only supplies financial resources to rapidly develop the technology, but it also provides the support structure through its vast network of business connections and business fellows to create accelerated pathways for transitioning the technology to market.”
“Intellectual property creation and protection is crucial in developing this cutting-edge technology to realize its true impact,” said Dr. Saurabh Biswas, executive director for TEES commercialization and entrepreneurship. His team is working closely with the TEES Clean Energy Incubator to support patent capture and utilization for MetPeel.
The project will also be supported by the SecureAmerica Institute, a TEES-led private-public partnership focused on advanced manufacturing, by providing adequate space to host MetPeel machinery in their new facility at the RELLIS campus as well as necessary resources and industry connections.
“MetPeel represents the best of TEES’ abilities to solve real problems for industry and society,” said Dr. Dimitris Lagoudas, deputy director for TEES. “Beyond technology development, TEES will directly support the development and use of this groundbreaking new manufacturing process through commercialization and product development assistance, test facilities, market identification and logistics. We look forward to the day MetPeel drastically reduces carbon emissions while creating new opportunities and jobs for American industries."