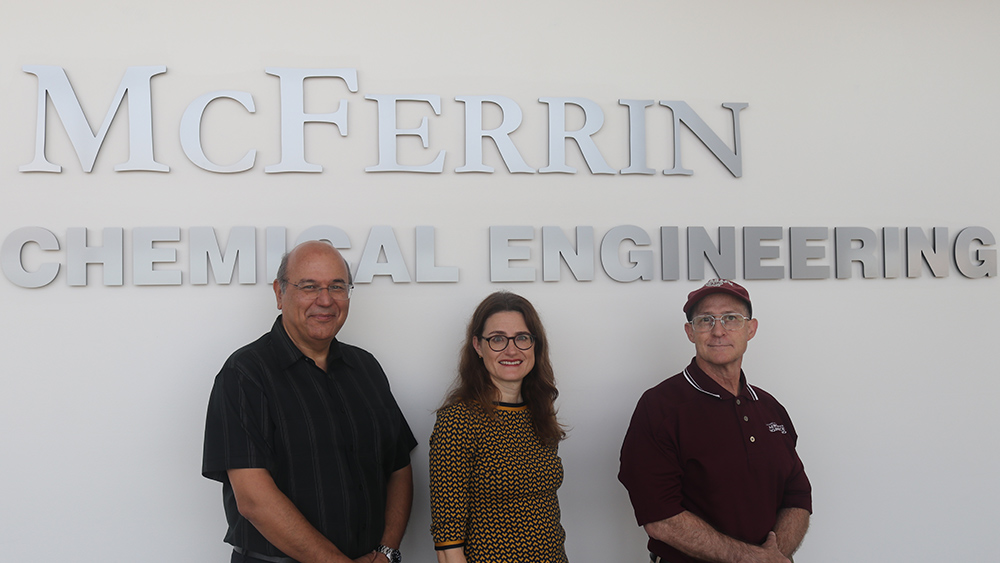
Texas A&M University researchers have discovered that when charging a supercapacitor, it stores energy and responds by stretching and expanding. This finding can be used to design new materials for flexible electronics or other devices that must be both strong and store energy efficiently.
Dr. Jodie Lutkenhaus, associate department head of internal engagement and chemical engineering professor, collaborated with Dr. Dimitris Lagoudas, professor of aerospace engineering and Dr. James Boyd, associate professor of aerospace engineering in a new paper published in Matter.
“We measured stresses that developed in graphene-based supercapacitor electrodes and correlated the stresses to how ions move in and out of the material,” Lutkenhaus said. “For example, when a capacitor is cycled, each electrode stores and releases ions that can cause it to swell and contract.”
Lutkenhaus said this repeated motion can cause the build-up of mechanical stresses, resulting in device failure. To combat this, her research looks to create an instrument that measures mechanical stresses and strains in energy storage materials as they charge and discharge.
“By gaining this critical insight, we might be able to design safer energy storage devices that will last longer.”
This instrument offers insights into measuring the mechanical behavior during an electrode's charging and discharging, which can be challenging to observe in real-time.
“We are pioneering experimental methods to measure the simultaneous electrochemical and mechanical response of electrodes,” Boyd said. “Our research is now moving from supercapacitors to batteries.”
Mechanical damage limits the cycle life of batteries, so new hardware and models are needed to interpret experimental measurements to separate the effects of mass diffusion, reactions, inelastic deformation and mechanical damage.
Batteries and capacitors can fail through the different effects of internal and external mechanical stresses. Internal stresses occur when batteries develop a repeated cycling of the device, while external stresses can result from impact or penetration of the device.
When these stresses happen, the battery needs to be able to withstand the damage. Lutkenhaus said it’s important to understand how mechanical stress develops in the electrochemical state of the device.
“We developed an instrument that can do just that, " Lutkenhaus said. “By gaining this critical insight, we might be able to design safer energy storage devices that will last longer.”
The research aims to develop energy storage devices that can bear structural loads and eventually replace carbon-fiber reinforced plastics that act as structural panels in aircraft, thus improving energy efficiency.
“This article is the outcome of an ongoing collaboration between chemical engineering and aerospace engineering scientists,” Lagoudas said. “This research provides a unique understanding of how nanomaterials can be used for lightweight and strong energy storage devices for aerospace applications.”
This research was supported by the Air Force Office of Scientific Research.