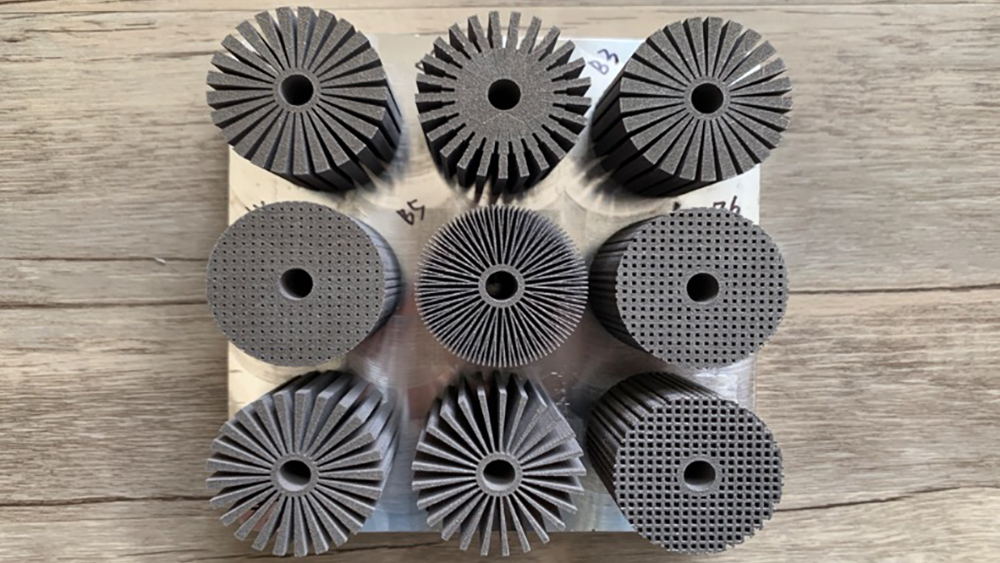
Researchers at Texas A&M University have established foundational design principles for composite phase change materials to store thermal energy rapidly. This breakthrough is expected to dramatically simplify the design process, allowing a near-optimal composite phase change material to be simply calculated without exhaustive computational fluid dynamic calculations or extensive iterative design.
Several previous studies have investigated the performance of thermal energy storage systems, although none have yet revealed insights into improving rate performance, optimization and prediction of performance until now.
Phase change materials store thermal energy as latent heat and are often integrated with high-thermal conductivity metals to make composites with high power density and large energy storage capacity. The fundamental question addressed by this research was how to design a composite phase change material that balances both energy density (how much energy can be stored — the equivalent of how far an electric vehicle could travel before running out of charge) and power density (how quickly energy can be stored — the equivalent of how long it would take to charge up an electric vehicle) without adding excess mass or volume.
This research, funded by the Office of Naval Research, provides a theoretical framework to design and optimize cylindrical composites with three figures of merit — minimization of temperature rise, maximization of the effective volumetric heat capacity and maximization of the effective heat capacity based on mass. The figures of merit developed in this work can assess the performance of most composite phase change material systems and help design future cylindrical composites while accounting for the thermal loads specific to the thermal storage application.
Importantly, the team experimentally demonstrated that treating the system as an effective composite allowed them to quickly simplify the calculations and predict near-optimal structures.
The team published its findings in the July issue of the International Journal of Heat and Mass Transfer and was led by Dr. Jonathan Felts, associate professor in the J. Mike Walker ’66 Department of Mechanical Engineering, and former mechanical engineering graduate student Achutha Tamraoarni.
Dr. Patrick Shamberger, associate professor in the Department of Materials Science and Engineering, leads the group as the principal investigator. Another collaborator on this project was Dr. Alaa Elwany, associate professor in the Wm Michael Barnes ’64 Department of Industrial and Systems Engineering. Former materials science and engineering doctoral student Alison Hoe, former industrial and systems doctoral student Chen Zhang and mechanical engineering doctoral student Nathan Malone were also instrumental in the discovery.