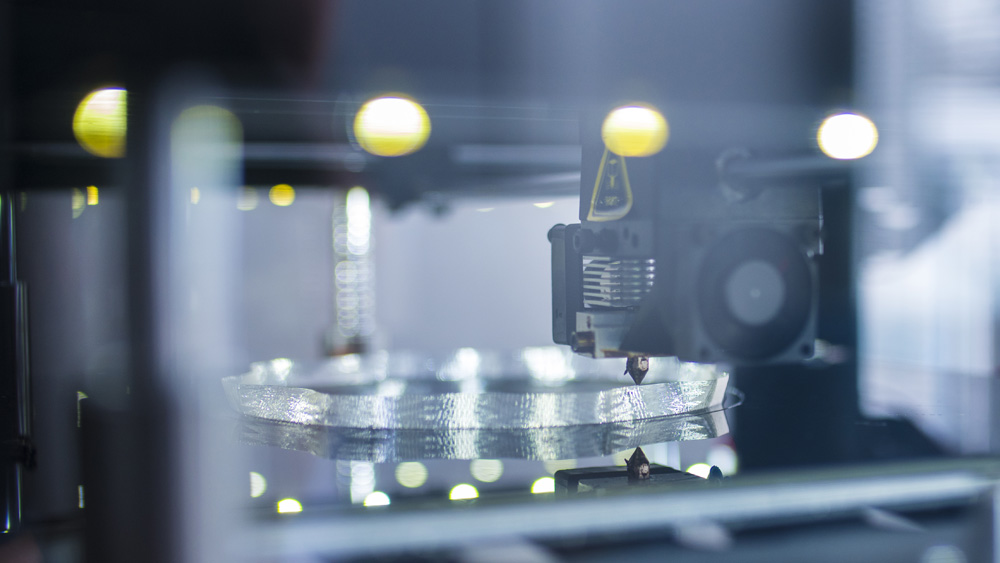
Dr. Zhijian “Z.J.” Pei and his intercollegiate team recently received the Future Manufacturing Research Grant from the National Science Foundation’s Future Manufacturing program, which funds researchers to develop new manufacturing capability that does not exist today. The focus of this research grant is to substitute products made from petroleum-based plastics or natural wood with biomass.
“Our idea is to use living matter, including fungi, algae, bacteria, plus agriculturally derived biomass and use 3D printing to make products,” said Pei, professor in the Wm Michael Barnes ’64 Department of Industrial and Systems Engineering at Texas A&M University.
While 3D printing with living matter, or bioprinting, is in use in health-related applications, Pei said his main applications are in packaging, furniture and construction industries.
“This is good for society and good for the environment,” Pei said. “Potentially, because these materials are locally available, we can create domestic jobs as well.”
The research team is interdisciplinary and includes experts from manufacturing, biology, civil and environmental engineering and mechanics. Other primary investigators of this project are Dr. Chiara Daraio from the California Institute of Technology (Caltech), Dr. Qiming Wang from the University of Southern California and Dr. Brian Shaw and Dr. Shawna Fletcher from Texas A&M. Among their collaborators are the Texas A&M Engineering Experiment Station’s (TEES) Workforce Development office, America Makes and the Association for Manufacturing Technology.
Each university brings a unique angle to the project. Pei is working on fungi-biomass composites, Caltech works on algae-biomass composites and the University of Southern California studies bacteria and biomass.
Along with the research, the team will create educational components as part of the grant including a textbook, an undergraduate student research program and training program for people working in the industry.
“Traditionally, manufacturing is mass production in one location,” Pei said. “It makes millions of parts and then ships them to different places. 3D printing is more suitable for distributed manufacturing — a small quantity of product is made at different places.”
Pei said support from departments, colleges and TEES is critical for successful proposals.