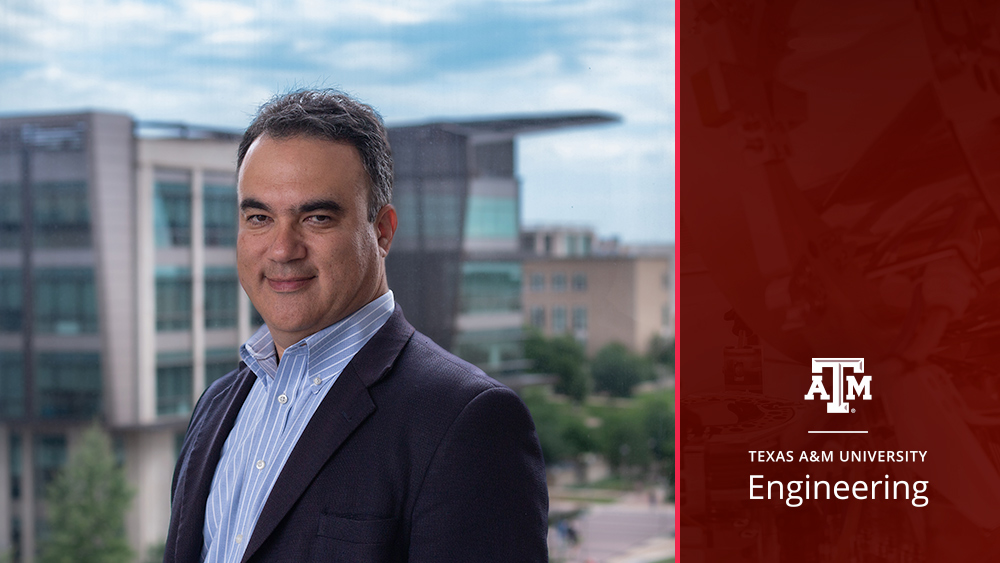
Researchers embarked on a multidisciplinary project to determine how cavitation bubbles within micro- or nano-structures could mitigate surface erosion and enhance the efficiency in microfluidic mixing devices, often used to quickly and effectively mix multiple samples.
Potential applications of the research findings include the creation of more efficient and resilient pumping machinery and implementation in portable, high-precision biological tests currently reserved only for laboratory settings. The research was recently published in Nature’s Scientific Reports journal.
The project was led by Dr. Guillermo Aguilar, James and Ada Forsyth Professor and department head in the J. Mike Walker ’66 Department of Mechanical Engineering at Texas A&M University.
Cavitation — the rapid formation and collapse of vapor bubbles in a liquid — is a widely studied field. This project sought to better understand the basic science of cavitation dynamics while also identifying potential applications.
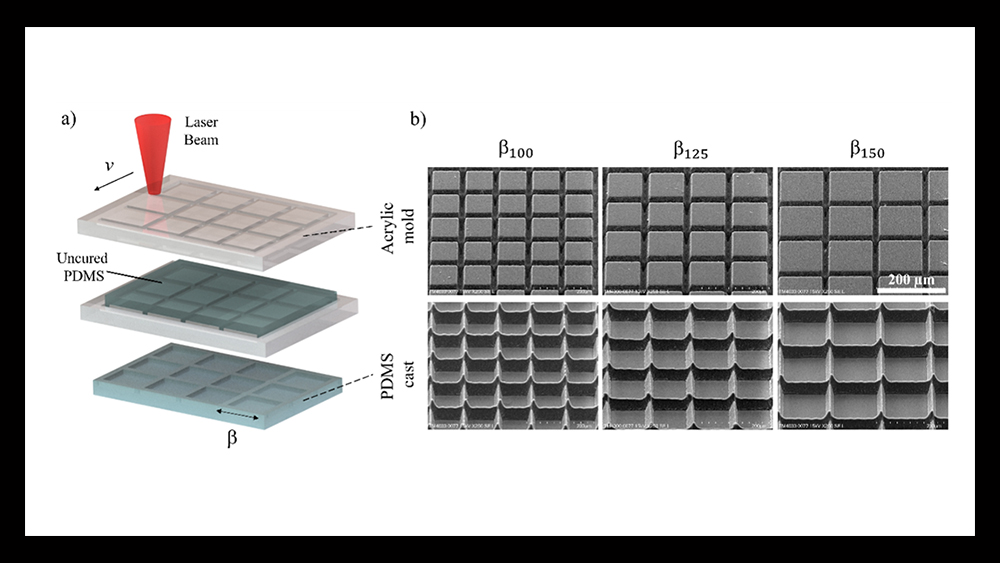
“Although cavitation has been studied extensively, the interaction of cavitation bubbles and jets with micro- or nano-structures and shockwaves are still an active area of research,” Aguilar said. “This study may also help us better understand and further develop new technologies such as erosion mitigation through surface micropatterning and development of efficient microfluidic mixing devices.”
Researchers used high-speed cameras equipped with microscope lenses alongside laser-induced cavitation to document the tiny bubbles, which typically boast the size of a single millimeter and last just one-tenth of a millisecond. Additionally, the project used multiple different lasers to serve various purposes throughout the research process, including a femtosecond laser to create the micropatterning in the target surface, a nano-second laser to induce cavitation and a continuous wave laser to perform particle tracking.
The methods enabled the team to trap air pockets in a microstructure surface and demonstrate how these air pockets could serve to greatly diminish the erosion typically caused by cavitation phenomena mechanisms. At the same time, the collapse of cavitation bubbles near micro- and nano-patterned surfaces enhanced the mixing of the contiguous fluid.
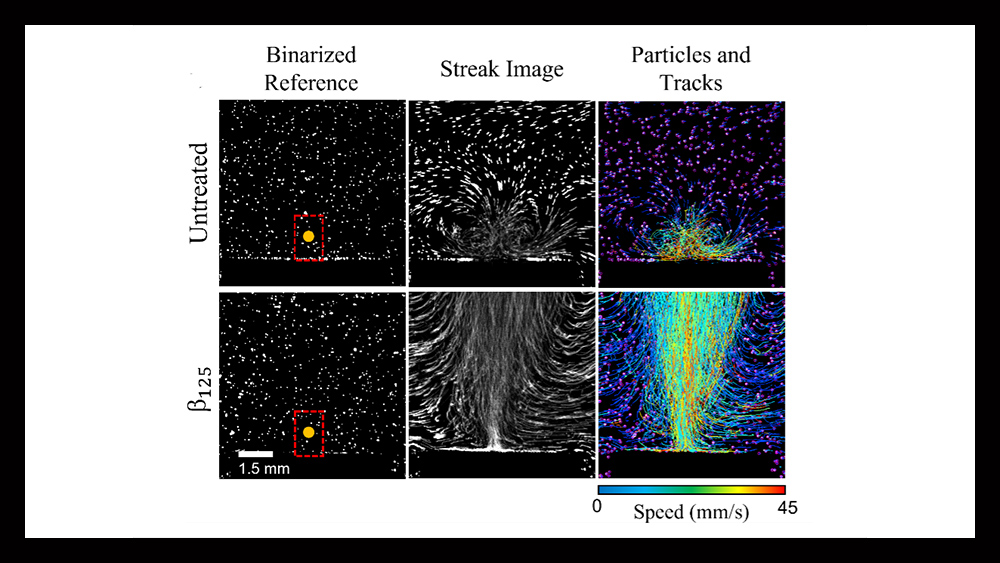
“We believe that this work has the potential to be the starting point for developing applications in microfluidics and erosion mitigation,” Aguilar said. “In the future, we could have commercial microfluidic devices that use this technique for in-situ, high-precision biological tests, which are currently restricted to laboratory environments. We also believe that this technique can be implemented to allow pumping machinery to work more efficiently and last longer, which would translate into cost reduction.”
One of the major challenges for this project came in the preparation. While assembling the team, a multitude of expertise in various disciplines was needed to effectively execute the project — a task for which Aguilar said mechanical engineers are well equipped.
“This can be described as a multidisciplinary project as not only fluids but also optics, photonics and material science,” Aguilar said. “As mechanical engineers, we have the broad knowledge base to tackle complex problems like this. Thus, this kind of multidisciplinary research relies heavily on teamwork.”
Collaborators on this project included Aguilar’s former doctoral students, Dr. Juan Carlos Gonzalez-Parra and Dr. Vicente Robles, alongside Dr. Natanael Cuando-Espitia from the Universidad de Guanajuato in Mexico.