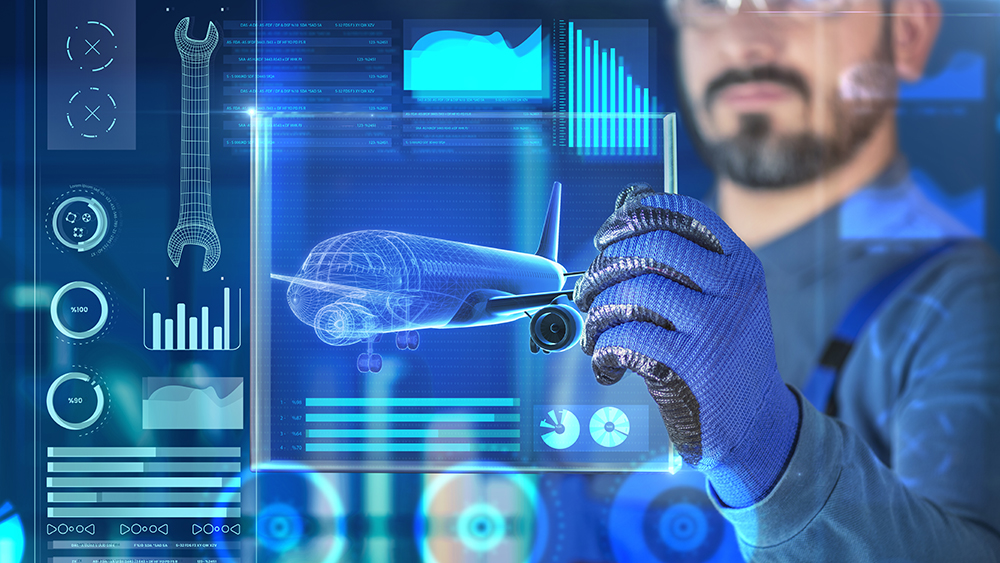
The Department of Defense’s grant to the Texas A&M Engineering Experiment Station will help place Texas at the forefront of aerospace manufacturing. |
Image: Getty Images
The digital era has transformed the future of manufacturing in Texas and across the nation, stressing a need to embed emerging smart technologies like advanced robotics and augmented reality into areas such as defense manufacturing. Recently, members of The Texas A&M University System formed a consortium with numerous partners to help meet this need and place Texas at the forefront of aerospace manufacturing.
In 2020, the Department of Defense (DOD) created the Defense Manufacturing Community (DMC) Support Program by the Office of Local Defense Community Cooperation to support consortiums as defense manufacturing communities that strengthen the national security industrial base. Through this program, the Texas A&M Engineering Experiment Station (TEES) was one of five teams awarded grants totaling about $25 million for the second round in 2021.
Their grant supports a $6,947,453 project to establish the Texas Defense Aerospace Manufacturing Community (TDAMC). TEES will lead this five-year program through the SecureAmerica Institute (SAI). The institute will inject targeted smart manufacturing skills and technologies into the diverse manufacturing portfolio of the Texas defense aerospace manufacturing ecosystem. The goal is to deliver outcomes in the areas of workforce development, structured networking and supply chain development, policy and economic development, and research and infrastructure.
“We were looking to do something where we could serve as a state agency and use our convening power to try to grow manufacturing initiatives and identify new customers, new opportunities, new programming — things that were less traditional college-type projects,” said Rob Gorham, SAI executive director. “Not just looking at how to make the manufacturing process better, but how to make manufacturing as an industry better.”
The National Association of Manufacturers says for every $1 spent in manufacturing, $2.79 is returned back to the economy. Gorham said this shows how much of an economic driver it is. The future of manufacturing, especially aerospace manufacturing that Texas leads by a large margin, is going to depend on these next-generation technologies.
For this project, Gorham and SAI teamed up with the Texas A&M Engineering Extension Service, known for workforce training and professional development, to form a collaboration with TEES Workforce Development, Texas A&M Engineering and numerous other partners throughout Texas. The Brazos Valley Economic Development Corporation (BVEDC) was a co-applicant for the grant and will serve as a community partner of TEES. The BVEDC will organize and manage various regionalization activities and interact with local economic development organizations from across the state to support the TDAMC, leveraging the assets of those communities to assist in awareness, talent and business retention, and expansion.
“Partnerships between state institutions and economic development organizations can prove extremely productive, and partnering with TEES from our community’s standpoint will enhance efforts for the defense and aerospace industries,” said Matt Prochaska, BVEDC president and CEO. “This is an example of how we’re building an ecosystem to serve an industry and increase our state’s competitiveness.”
Gorham said they looked for a region involved in industry that included demographics with different variables where they could deploy the smart manufacturing. For this, they chose the Texas Triangle (the region consisting of the Dallas-Fort Worth, Houston, San Antonio and Austin metropolitan areas) and the Gulf Coast 75 miles inward, all the way down to the Rio Grande Valley. Here, the TDAMC aims to infuse smart manufacturing tools and processes into the region to solidify Texas’ leadership role in the global aerospace manufacturing economy and beyond.
Currently, there are only 11 of these DOD DMC designations in the nation, including the one with TEES, which is the only one in Texas. Gorham said this designation could also open up the state to many other opportunities, now and in the future.
“Because of the designation, it's putting us in competitive positions for new programming coming out of the federal government,” he said. “It's also allowing us to use our designation as proof that we have the capability at TEES to reach into different regions across the state and to start working on some of these mission-driven needs that we have at a state level.”
At this early stage, the consortium team is working on a handful of deliverables to provide to the DOD, including a detailed execution plan. They have created a 10-step plan with specific tasks to accomplish TDAMC objectives across the three phases: initialize, develop and deploy, and refine and scale. To help with this plan, they will create a threat-casting exercise where they project the state of Texas and the specified region 10 years into the future, trying to imagine what things like energy, transportation and aerospace manufacturing will look like.
“Aerospace is our topic, so that'll be what we're most focused on,” Gorham said. “And from there, we’ll start to identify existing gaps that are going to depend on the adoption of smart manufacturing for us to be able to realize a future that we're defining. So that's going to be an awesome opportunity for us to really project and help the community get to that future state in a successful way.”
Gorham said the program would continue to position Texas as a leader in manufacturing, especially in aerospace. Instead of trying to chip away at adoption of these next-generation technologies at the individual company level, it will bring manufacturers together to understand what standards and technical gaps exist and economic considerations that need to be thought through. In the end, Gorham adds that just like Google made people’s lives easier by understanding how to find information that's relevant to the questions being asked, he hopes the consortium they’re building is going to serve the same way except with manufacturing in mind.
“There's so much manufacturing information out there — there's good information, there's misinformation, there's confusion on how we embrace and adopt these new processes. There's also competition between service providers and equipment providers and confusion around how to integrate processes into factories and production operations,” he said. “That's what we're going to help try to bring clarity to. Instead of everyone trying to figure that out for themselves, we want to sort of standardize the approach and the answers so that everyone can make a decision from an equal playing ground. And we think that's a huge value proposition.”
In 2020, the Department of Defense (DOD) created the Defense Manufacturing Community (DMC) Support Program by the Office of Local Defense Community Cooperation to support consortiums as defense manufacturing communities that strengthen the national security industrial base. Through this program, the Texas A&M Engineering Experiment Station (TEES) was one of five teams awarded grants totaling about $25 million for the second round in 2021.
Their grant supports a $6,947,453 project to establish the Texas Defense Aerospace Manufacturing Community (TDAMC). TEES will lead this five-year program through the SecureAmerica Institute (SAI). The institute will inject targeted smart manufacturing skills and technologies into the diverse manufacturing portfolio of the Texas defense aerospace manufacturing ecosystem. The goal is to deliver outcomes in the areas of workforce development, structured networking and supply chain development, policy and economic development, and research and infrastructure.
“We were looking to do something where we could serve as a state agency and use our convening power to try to grow manufacturing initiatives and identify new customers, new opportunities, new programming — things that were less traditional college-type projects,” said Rob Gorham, SAI executive director. “Not just looking at how to make the manufacturing process better, but how to make manufacturing as an industry better.”
The National Association of Manufacturers says for every $1 spent in manufacturing, $2.79 is returned back to the economy. Gorham said this shows how much of an economic driver it is. The future of manufacturing, especially aerospace manufacturing that Texas leads by a large margin, is going to depend on these next-generation technologies.
For this project, Gorham and SAI teamed up with the Texas A&M Engineering Extension Service, known for workforce training and professional development, to form a collaboration with TEES Workforce Development, Texas A&M Engineering and numerous other partners throughout Texas. The Brazos Valley Economic Development Corporation (BVEDC) was a co-applicant for the grant and will serve as a community partner of TEES. The BVEDC will organize and manage various regionalization activities and interact with local economic development organizations from across the state to support the TDAMC, leveraging the assets of those communities to assist in awareness, talent and business retention, and expansion.
“Partnerships between state institutions and economic development organizations can prove extremely productive, and partnering with TEES from our community’s standpoint will enhance efforts for the defense and aerospace industries,” said Matt Prochaska, BVEDC president and CEO. “This is an example of how we’re building an ecosystem to serve an industry and increase our state’s competitiveness.”
Gorham said they looked for a region involved in industry that included demographics with different variables where they could deploy the smart manufacturing. For this, they chose the Texas Triangle (the region consisting of the Dallas-Fort Worth, Houston, San Antonio and Austin metropolitan areas) and the Gulf Coast 75 miles inward, all the way down to the Rio Grande Valley. Here, the TDAMC aims to infuse smart manufacturing tools and processes into the region to solidify Texas’ leadership role in the global aerospace manufacturing economy and beyond.
Currently, there are only 11 of these DOD DMC designations in the nation, including the one with TEES, which is the only one in Texas. Gorham said this designation could also open up the state to many other opportunities, now and in the future.
“Because of the designation, it's putting us in competitive positions for new programming coming out of the federal government,” he said. “It's also allowing us to use our designation as proof that we have the capability at TEES to reach into different regions across the state and to start working on some of these mission-driven needs that we have at a state level.”
At this early stage, the consortium team is working on a handful of deliverables to provide to the DOD, including a detailed execution plan. They have created a 10-step plan with specific tasks to accomplish TDAMC objectives across the three phases: initialize, develop and deploy, and refine and scale. To help with this plan, they will create a threat-casting exercise where they project the state of Texas and the specified region 10 years into the future, trying to imagine what things like energy, transportation and aerospace manufacturing will look like.
“Aerospace is our topic, so that'll be what we're most focused on,” Gorham said. “And from there, we’ll start to identify existing gaps that are going to depend on the adoption of smart manufacturing for us to be able to realize a future that we're defining. So that's going to be an awesome opportunity for us to really project and help the community get to that future state in a successful way.”
Gorham said the program would continue to position Texas as a leader in manufacturing, especially in aerospace. Instead of trying to chip away at adoption of these next-generation technologies at the individual company level, it will bring manufacturers together to understand what standards and technical gaps exist and economic considerations that need to be thought through. In the end, Gorham adds that just like Google made people’s lives easier by understanding how to find information that's relevant to the questions being asked, he hopes the consortium they’re building is going to serve the same way except with manufacturing in mind.
“There's so much manufacturing information out there — there's good information, there's misinformation, there's confusion on how we embrace and adopt these new processes. There's also competition between service providers and equipment providers and confusion around how to integrate processes into factories and production operations,” he said. “That's what we're going to help try to bring clarity to. Instead of everyone trying to figure that out for themselves, we want to sort of standardize the approach and the answers so that everyone can make a decision from an equal playing ground. And we think that's a huge value proposition.”