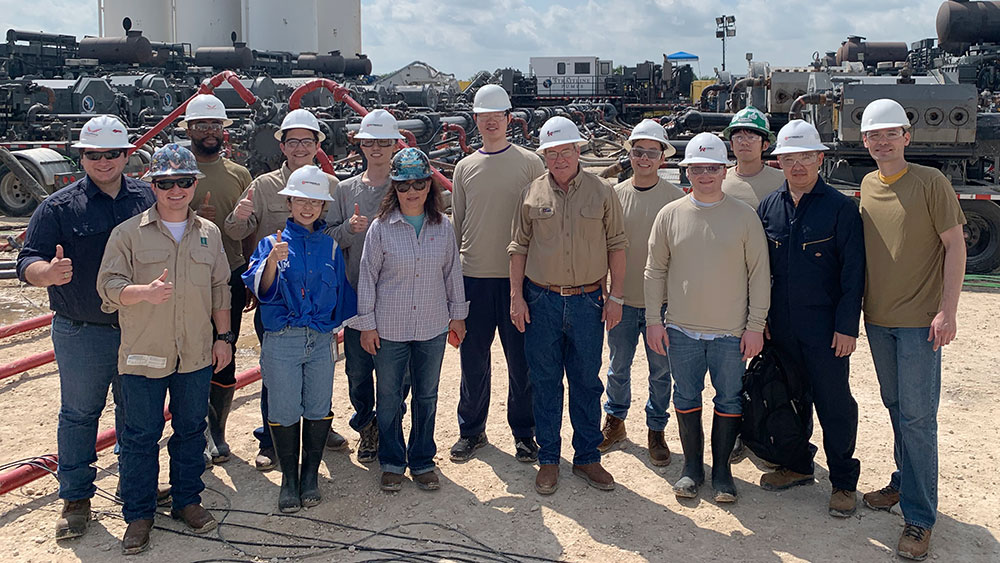
The following is a first-person account by Dr. Dan Hill, Regents Professor at Texas A&M University, of a field trip he took his graduate students from the Harold Vance Department of Petroleum Engineering on in May 2021 to share with them what a fracturing treatment is like on site.
An old saying states that a picture is worth a thousand words. In these times, we can extend that to say a video is worth a thousand pictures. However, no picture or video is as instructive as doing or seeing an engineering activity in person, which is why I invited students from my PETE 602 Well Stimulation class to witness part of a multi-stage hydraulic fracturing treatment performed by Ironroc Energy last May. We were joined by McCain Engineering Chair Dr. Ding Zhu and some students from her course, PETE 636, Horizontal and Multilateral Wells.
Hydraulic fracturing is a process in which large volumes of water and sand are injected into oil- or gas-bearing rock at high enough pressure to break the rock. The injected sand/water slurry creates an extensive network of fractures in shale-type rocks, and the sand holds these fractures open so that oil and gas can flow to the well. Without hydraulic fracturing, production from the vast resource of shale in the U.S. and elsewhere is not possible. Hydraulic fracturing, along with horizontal drilling, is the enabling technology that has resulted in the U.S. being the leading producer of oil and gas in the world.
In my 39 years of teaching petroleum engineering, I have taken many students on many field trips like this one, and the students invariably come back with a much better appreciation of the technology being implemented. One of my students, Alex Fojtasek, said it allowed him to "bridge the gap between what was learned in class and what is practiced in the field." It's critical for students to make these kinds of connections as they gain knowledge.
Our host for this field trip was Mike McCoy, petroleum engineering class of ’83 (and Department Head Dr. Jeff Spath’s former classmate), who is the chief operations officer of Alpine Energy, the parent company of Ironroc. Mike has been overseeing hydraulic fracturing operations all over the world his entire career. When I reached out with blind phone calls to arrange a trip, he answered within minutes. We cannot have experiences like this for our students without this kind of generosity.
Ironroc Energy was fracturing its Austin Chalk wells Swedish Chef 2H and 3H. The two wells were being zipper-fractured, meaning a fracture stage would be pumped on one well while the wireline setting of plugs using perforating guns (a 'plug-and-perf') would be conducted on the other, then the well processes would be swapped and the procedures continued.
The well site in Washington County was less than an hour’s drive from the Richardson building on the Texas A&M University campus. When we arrived, our tour began with a safety meeting, then Chris McCoy ’12, senior operations engineer for Ironroc, led us around the pad site. Chris is Mike's son, so two generations of generous Aggie petroleum engineers were with us that day.
Some of the major components we saw were the high pressure (15,000 psi rating) manifold connecting 23 fracturing pumps of at least 2000 horsepower each, the large proppant storage bins with pump trucks in the foreground, and the two wellheads (one maroon, one white). The maroon wellhead was rigged for pumping a fracturing stage and the white wellhead rigged for wireline plug and perforating operations.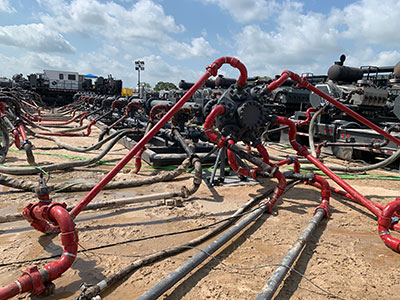
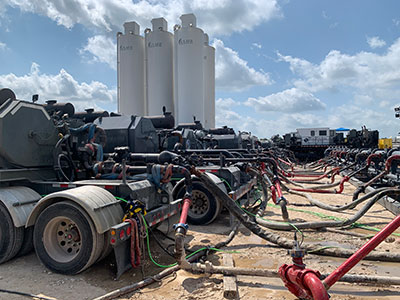
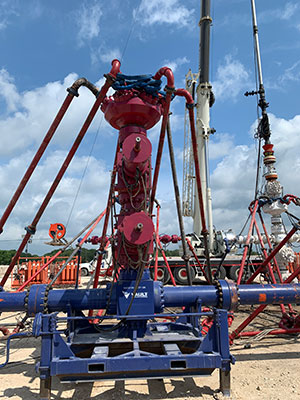
After we toured the entire site, we were shown some of the downhole equipment used in plug and perforating multi-stage fracturing completions. Chris described the features of a modern fracturing plug to the students. These plugs are made out of composite materials that are easy to drill out after the fracturing operations. One of my doctoral students, Tohoko Tajima, discovered these plugs are light enough for anyone to lift.
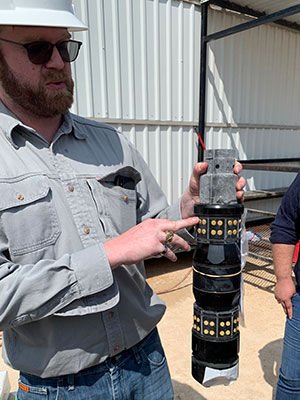
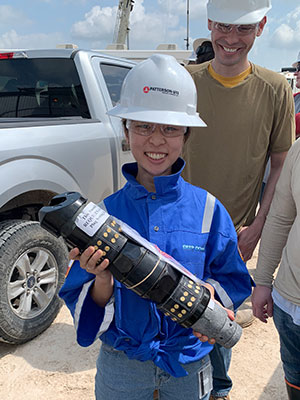
After our site tour, we joined Ironroc and service company engineers in the monitoring van as they began pumping a fracturing stage. We observed pumping at 93 barrels per minute with a surface pressure around 10,000 psi for over an hour as most of a fracturing stage was pumped. Mike and a service company fracturing engineer monitored the progress of the fracturing stage on computers while it happened. Thirty-three stages of fracture treatments were pumped into each well, with a total of 15,840,000 pounds of sand, carried in slick water, injected into each well.
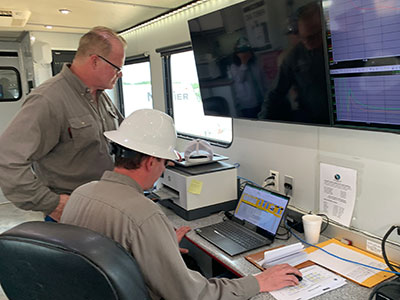
Our tour concluded in typical oilfield fashion – with a lunch cooked onsite by one of the service companies involved (Innospec Oilfield Services, a chemical supplier). Hamburgers and grilled sausage with all the trimmings were enjoyed by all.
When faculty lecture about oil and gas technology, we convey concepts and teach design methods. But when my student has held a fracture plug in her hands, she knows I am talking about a two-foot-long, 20-pound composite device that has been highly engineered for a specific purpose when I lecture about plug-and-perf well completions.
This is why it's so important for petroleum engineers go out to the field, we get to see the reality of our discipline.