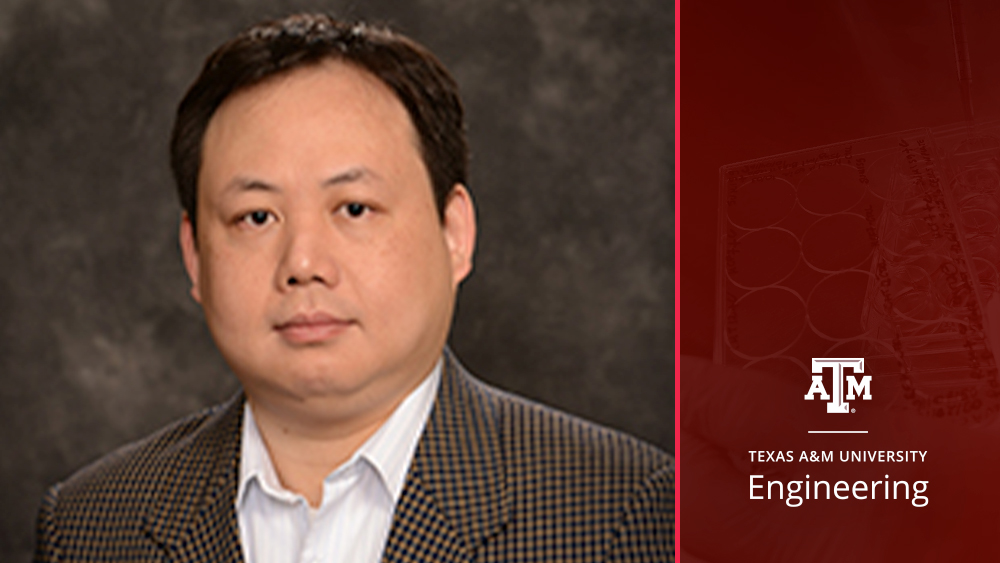
Similar to how sculptors use chisels to create esthetic shapes on a piece of marble, designers of electronic chips can use powerful, narrow beams of light to create electronic circuitry at the microscale. This process is known as lithography, and Texas A&M University researchers are working to improve this technique.
Photolithography is used in the microfabrication of electronics to create intricate patterns or structures layer by layer. A photoresist sits on a photomask. Similar to the negative of a photo film, the photomask is the complementary design of the circuit that you want to achieve. When light falls on the photoresist, the light dissolves the exposed surfaces (the areas not covered by the mask), leaving behind the desired circuit.
A similar approach is applied to construct micromechanical and microbiomedical devices. However, to increase the complexity and functionality of these microscale devices, extending the capability of lithography from 2D to 3D structures becomes a need in this decade.
Addressing this technological need, Dr. Sy-Bor Wen, associate professor in the J. Mike Walker ’66 Department of Mechanical Engineering, is fine-tuning the technology needed to use a light pulse that flickers at a frequency of one-billionth of a second for 3D lithography. Funded by the National Science Foundation, this study was recently accepted for the American Society of Mechanical Engineers’ Conference.
“The main advantage of the developing method is the ability to use millions of light beams simultaneously to generate 3D patterns,” said Wen. “This shows great potential in different 3D photonics, 3D electronic and 3D biomedical uses but suffers from very low throughput.”
The process is critical when developing 3D electronics, mechanics and biomedical structures because of the associated high spatial resolution and high speed with millions of mini light beams. State-of-the-art 3D fabrication is mainly based on layer-by-layer stacked 2D fabrications, which has low throughput, and limited geometric configurations can be fabricated.
Using Wen’s method, through a combination of spatial light modulators and microlens arrays, a single femtosecond laser pulse can be split into more than one million mini rays that can be turned on or off with phase control. Under appropriate manipulation of these rays, thousands of focal spots at different locations and depths within 3D blocks, called voxels, can be generated for patterning different photopolymers.
“By using these thousands of focal spots, 3D fabrication can be achieved with orders of higher speed than traditional 3D fabrication with deep micron level resolution and allows construction of complicated microscale 3D structures,” said Wen. “Moreover, light absorption induced with the femtosecond laser pulse allows fabrication to be conducted at exact depths, allowing other layers to remain intact on 3D objects through multiphoton absorptions.”
Currently, these preliminary results are solely for inorganic structures extensively in rapid prototyping and manufacturing. Wen’s next goal is to transfer this technology into creating organic scaffolds that can be used in human tissue regeneration so that they can be implanted in the body at sites needing repair.
Wen and his fellow contributor, Dr. Vladislav Yakovlev, professor in the Department of Biomedical Engineering, are still testing this hypothesis and hope to bring in other researchers to develop this technology.