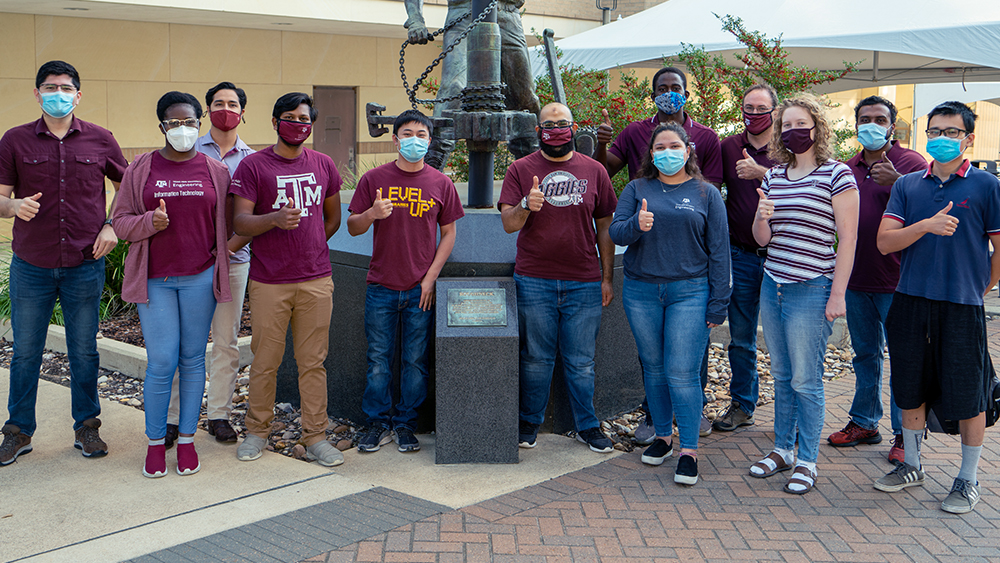
After impressing judges with their hard work and creativity in the 2020 NASA Moon to Mars Ice and Prospecting Challenge, an interdisciplinary team of 13 engineering students from the College of Engineering at Texas A&M University was invited back to the 2021 competition. The 2020 NASA challenge encouraged these Aggies to design and build an impressive next-generation drilling rig prototype for space use. They ended up as one of only 10 teams selected to showcase their efforts at NASA Langley with a video submission.
Both the moon and Mars feature underground ice deposits, so NASA wants to harvest this resource for energy, agriculture and other uses. The students were asked to create a drilling and ice-harvesting system that could be used remotely with minimal human interaction.
They devised a plan that incorporates standard drilling systems on Earth, where sensors and actuators are found on and behind the drilling bit, but included an adjustment for use in an airless environment. The Aggie team then constructed a prototype drilling rig that is self-deployable, automated and can perform more than one operation without changing any equipment.
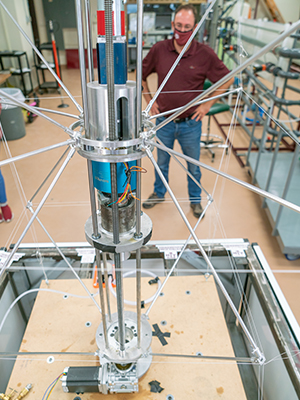
Their creation, the Drilling and Extraction Automated System, nicknamed DREAMS, has four main benefits that make it perfect for use on the moon or Mars.
The rigging is an advanced tensegrity structure made of a strong but lightweight system of rods, cables and rotary motors. This configuration reduces the rig’s weight and allows it to unfold or fold itself up as needed for deployment.
The drilling system uses a short drill bit length connected to drill pipes, so it can potentially carve through solid rock and reach estimated depths of hundreds to thousands of meters.
The drilling, heating and extraction components needed for prospecting into the soil for ice are one integrated system, meaning they can work individually or together to save time and expense.
The computer hardware, controls and algorithms work together in an automated drilling system, one that can assess, measure and ‘feel’ its way through the different materials it travels through, speeding up or slowing down as needed without human intervention to maintain safe operations.
The students faced several challenges during the development of DREAMS. Since tensegrity structures haven’t been applied to drilling before, the students worked with the SuSu and Mark A. Fischer ’72 Engineering Design Center staff in the Zachry Engineering Education Complex to 3D print unique parts and components for testing before making final parts. They situated a heating element right behind the drilling bit to be activated when data indicated they were drilling in ice but found the heating element melted the delicate nano-sized wiring of the monitoring system, also located behind the drill bit. They overcame this problem by contacting professors in mechanical and chemical engineering who suggested an insolating chemical paint to protect the wiring.
The students were guided by several faculty members. Dr. Eduardo Gildin from the Harold Vance Department of Petroleum Engineering advised them on automated control systems and helped with fundraising. Dr. George Moridis, also in petroleum engineering, had previous work experience with NASA and mentored them on fluid flow and harvesting frozen materials. Aerospace engineering and ocean engineering professor, Dr. Robert Skelton, a renowned expert on tensegrity, provided advice with the rig configuration. Petroleum engineering associate professor of practice Dr. Sam Noynaert offered his experience with student competitions and drilling systems.
“They came up with ideas that are amazing,” said Gildin. “It was the students who suggested in the very beginning to create the tensegrity components using 3D printing so they could assemble and check measurements as things progressed.”
The students had separate meetings apart from their mentors that were led by team leader Mohamed Khaled. Ideas were encouraged from every student. In their meetings with faculty, the team dealt with the details of how to integrate their ideas into one fully functioning machine. Now that they have been invited back for the next-level challenge, the Aggies are increasing their effort. Gildin remarked that their creations are “already patent-level”.
“One of the main things I learned through this experience is that these students, regardless of graduate or undergraduate level, have exceptional ideas,” said Gildin. “They are here to learn, and they are dedicated students.”
Original 2019-2020 Team members (listed alphabetically):
- Ayodeji (Ayo) Avis Adeniran, doctoral student in mechanical engineering
- Muhao Chen, doctoral student in aerospace engineering
- Jessica Ezemba, undergraduate student in mechanical engineering
- Mohamed Khaled (team lead), doctoral student in petroleum engineering
- Emily Kincaid, undergraduate student in mechanical engineering
- Le Linh, master’s student in petroleum engineering
- Thomas J. Lopez, doctoral student in interdisciplinary engineering
- Ahmed Madi, undergraduate student in mechanical engineering
- Luis Rodriguez, master’s student in mechanical engineering
- Srivignesh Srinivasan, master’s student in mechanical engineering
- Alkassoum Toure, master’s student in petroleum engineering
- Teresa Valdez, undergraduate student in computer engineering
- Uthej Vattipalli, master’s student in civil engineering