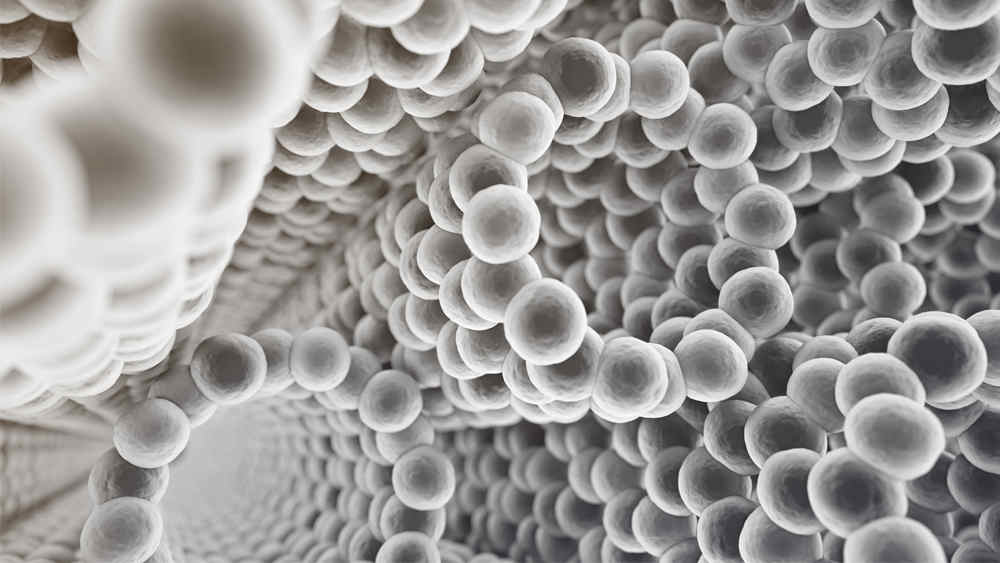

Asadi is an assistant professor in the Department of Engineering Technology and Industrial Distribution at Texas A&M University, and his project is funded by the National Science Foundation.
“My research is like tailoring,” Asadi said. “You put fabrics together and sew them to make something out of it with the desired properties and level of performance in your mind. These nanomaterials are the nanothreads.”
Carbon fiber reinforced polymer (CFRP) composites, the most commonly used in the aerospace industry, are able to withstand the highest load-to-weight ratio, which makes them highly desirable for aerospace and defense applications.
Unfortunately, the current CFRPs are expensive – both in carbon production cost and time needed to manufacture them – and have reached a plateau in their strength capabilities. Additionally, while studies suggest that integrating carbon nanotubes into CFRPs can overcome these strength limitations, the process includes invasive treatment that leads to uneven distribution of the nanotubes and damaging carbon fibers that can actually counterproductively weaken the final product.
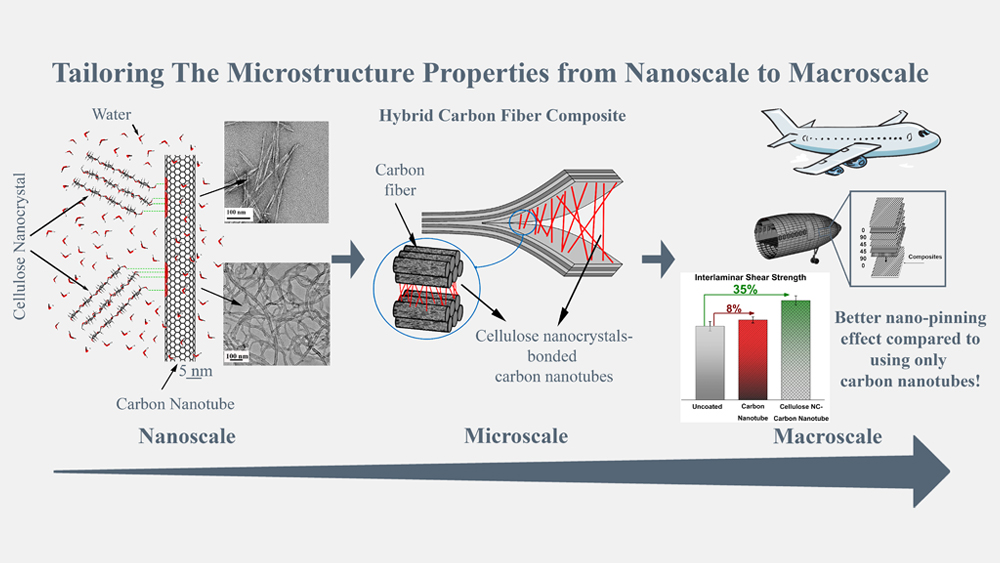
In response to this, Asadi and his team have established a new method of manufacturing that utilizes cellulose nanocrystals in place of chemicals, time- and cost-ineffective processes.
“The new process enables the production of nanostructured hybrid CFRP composites at a large scale with desired structure and performance with fewer processing steps,” Asadi said.
Along with reducing the time and expense associated with making these composites, the process opens the door for more customizable materials.
“Right now, we have very large and bulky materials, and we start to cut them and make something out of them," said Asadi. "If we achieve this process successfully, we can start to build complex structures from the nanoscale. We would be able to engineer structures from the bottom to the top. So this is exciting for me because, first of all, you are mimicking nature. And second of all, you can create structures with desired properties without wasting any material.”