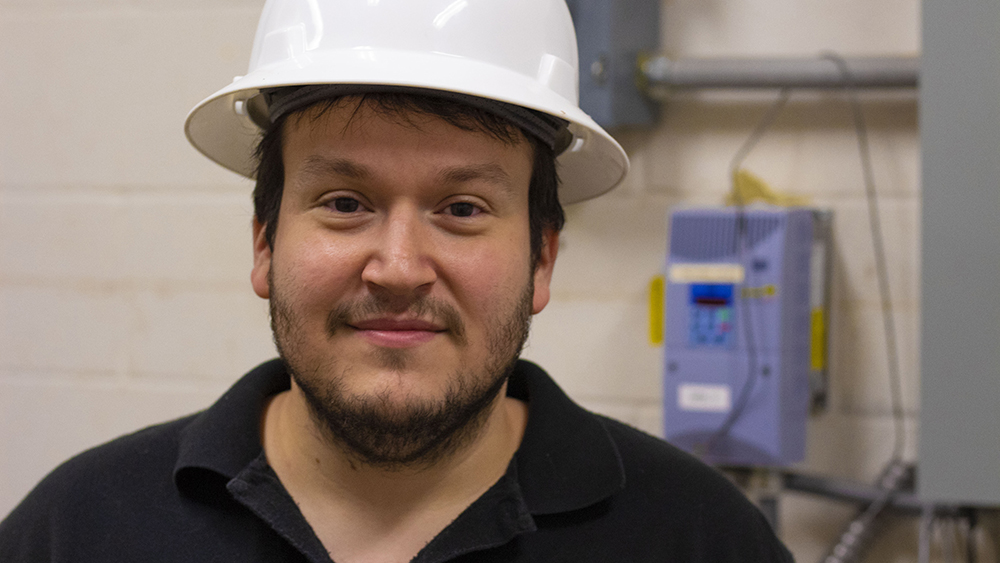
On any given day, you might walk by the 10-story Richardson building and think of it as just one of the taller structures on the Texas A&M University campus: stately and unsurprising. But did you know a vertical lab stands inside the building, one that is taller than the building you see on the outside?
Graduate student Omer Kaldirim knows all about this hidden facility. He recently led a team of students through an intensive upgrade of the lab, one of the most unique labs at Texas A&M and one of the tallest academic research flow loops, or piping systems designed for studying fluid and gas interactions, in the world.
“People wonder where I’m coming from when I come up from the basement all the time,” said Kaldirim. “Not many of our undergrads, grads and not even all the faculty know about Tower Lab.”
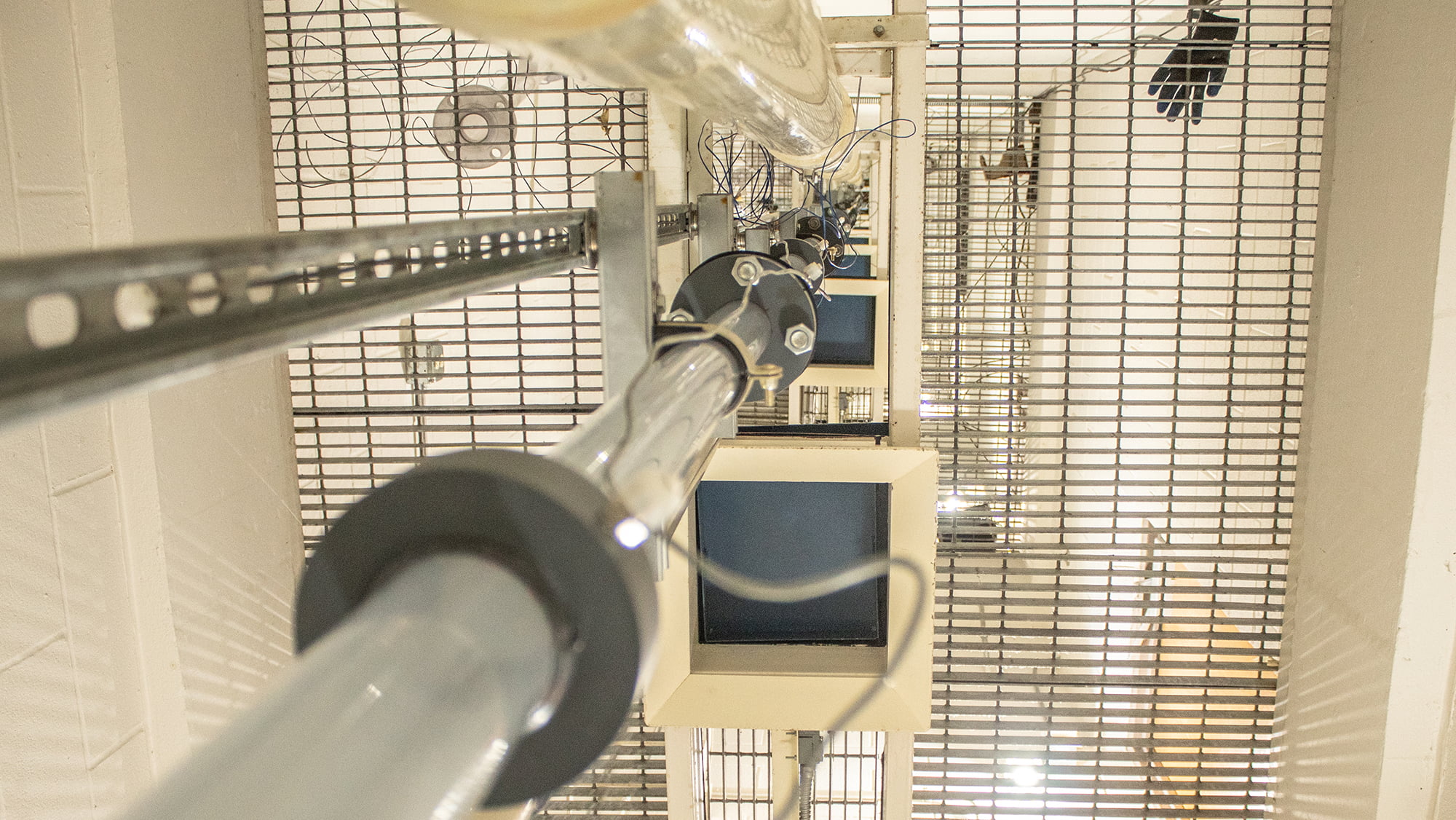
This large-scale flow loop research lab, affectionately known as Tower Lab, is a 142-foot vertical assembly of clear pipes, steel pipes, pumps, tanks and other equipment tucked away inside a hollow column of space within the core of the Richardson building. An access door on every floor allows entry, but because of the tall, unbroken piping loops and pump systems, there is nothing between the roof and the basement to stand on except a series of open grating panels and a very long ladder. While not quite a ‘Tower of Terror,’ looking up or down inside Tower Lab, nearly half a football field in height, can easily mess with depth perception.
Why have such a tall vertical lab?
Oil and gas exploration efforts usually begin with a vertical well drilled into the earth. These initial wellbores are often thousands of feet deep and, since they can be the first contact with a reservoir, the place where challenging pressure changes, fluid movements and accidents usually occur. For example, trapped gas in a reservoir will want to enter the well, travel up and escape to the surface where it can expand in a dangerous blowout situation. Drilling muds are circulated down inside the drill pipe and back up inside the casing around the drill pipe to force gasses to stay within the reservoir.
Tower Lab’s height and equipment help researchers understand how compressed reservoir gasses react if they manage to invade the different types of muds in the well. The lab features clear two- and four-inch diameter pipes so that gas behaviors can be visually studied and measured.
“Experiments in Tower Lab can be scaled up to match the actual drilling conditions of using 19- to 22-inch diameter pipes in one- to 12-kilometer depths,” said Kaldirim. “Right now, I’m outfitting it for use in research to improve existing deepwater drilling well control practices.”
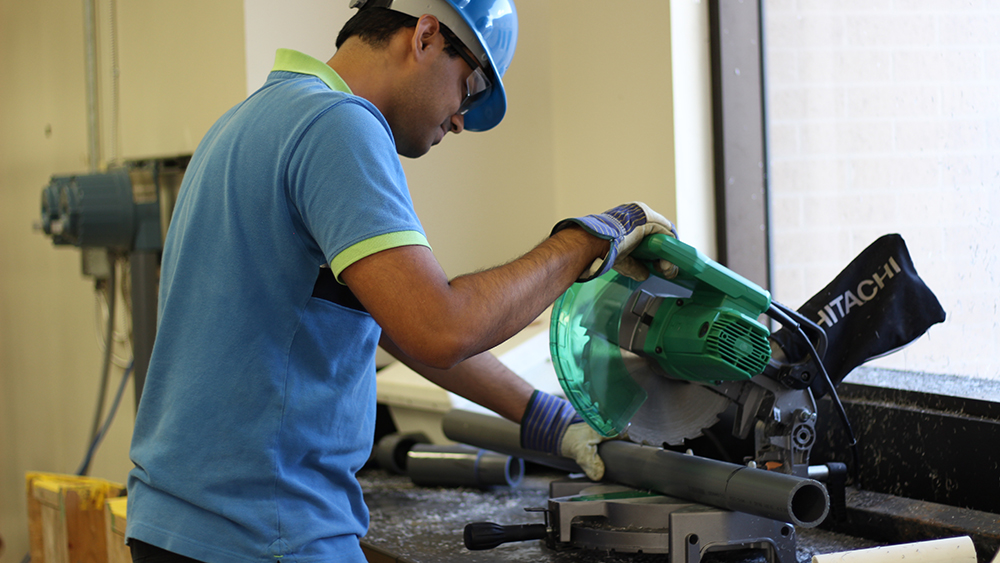
Kaldirim is a member of a team led by Dr. Jerome Schubert and Dr. Rashid Hasan, faculty in the Harold Vance Department of Petroleum Engineering. Their work is part of a joint project with Louisiana State University to improve deepwater drilling safety. The project began in 2018, funded with a $4.9 million award from the Gulf Research Program of the National Academies of Sciences, Engineering and Medicine.
“The Tower Lab upgrade was paid for with a portion of that,” said Kaldirim. “We needed to make the lab more versatile and work better for the riser gas research.”
Risers are the large vertical pipes a drilling assembly travels through between offshore rigs and the seafloor below. Most operations have a blowout preventer on the seabed and trust that drilling fluids, like the mud, and this blowout-prevention device will keep gasses from coming up to the surface. But in 2010, reservoir gasses invaded the riser of the Macondo well operation out in the Gulf of Mexico, leading to a deadly blowout explosion, the destruction of an offshore rig and a catastrophic oil spill.
“Shale may be slowing down the deep well drilling offshore, but it’s still there,” said Kaldirim. “Companies are interested in this research. No one wants uncontrolled riser gas to cause another blowout. We’re just now acquiring a lot of information on safer, managed pressure drilling methods in controlling riser gas and improving well control practices. This lab can prove concepts and prove which ideas don’t work.”
Kaldirim is a Ph.D. student with a master’s degree in petroleum engineering and a bachelor’s degree in mechanical engineering. He has experience working with oil companies and even did short-term work at well sites where he acquired a deep respect for drilling processes. Yet the Tower Lab upgrade was a different kind of education.
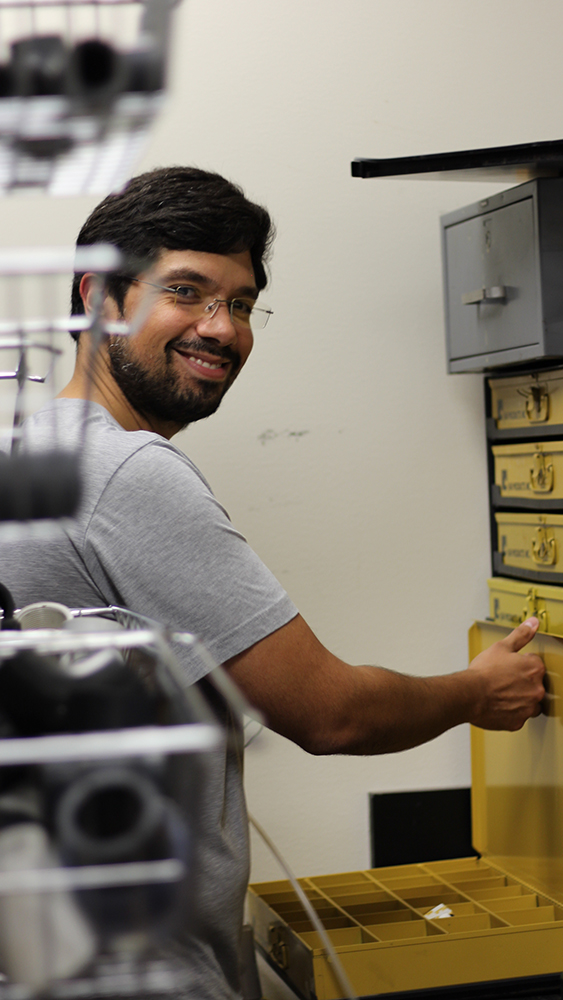
“Redoing this lab has been a huge learning experience,” he said. “Whatever I didn’t know, I investigated. Whatever I couldn’t do, I outsourced, yet still tried to help with. You can’t be shy in the petroleum industry. You engage people in what you’re trying to do and, in turn, they become interested in you.”
Kaldirim spent the summer and fall 2019 semesters and part of the spring 2020 semester assembling new pipes and changing out equipment. He also connected with other students who were willing to help him, especially Kaushik Manikonda, Pedro Sousa, Mohamed Shafik Khaled, and Dinara Dussenova. Together, with the help of Richardson building facilities coordinator John Maldonado, they recalibrated systems, tested transducers, upgraded meters, and moved tanks and separators to different heights. The upgrade will produce higher flow rates and gain better accuracy in gas expansion experiments and flow experiments for the managed pressure drilling research he will complete this year.
“When people find out about Tower Lab, there’s interest,” said Kaldirim. “To lose Tower Lab would be to lose an opportunity for future research and to make a difference in oil and gas safety. We have to market it, make sure people know it’s here.”