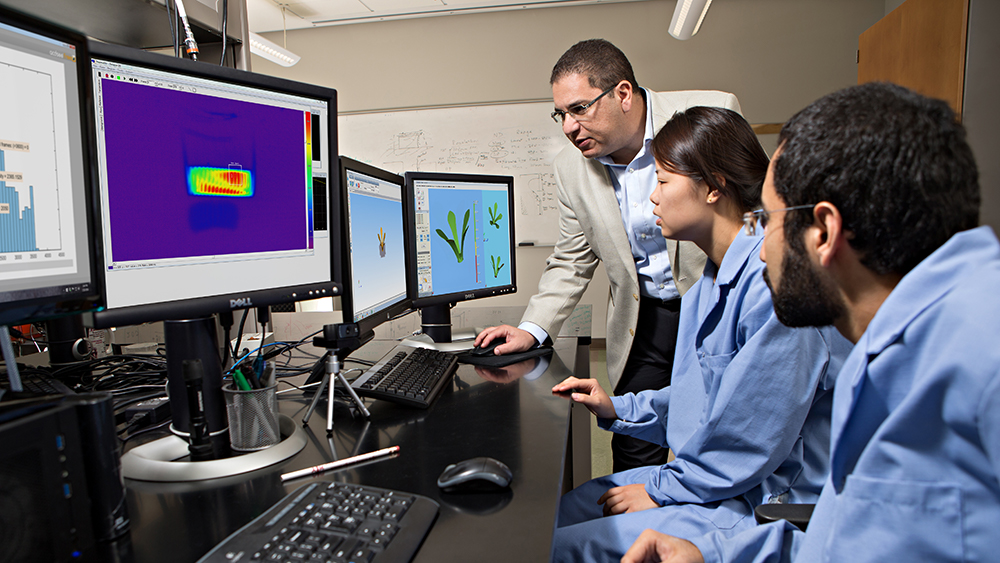
Dr. Alaa Elwany, assistant professor in the Department of Industrial and Systems Engineering at Texas A&M University, has received the National Science Foundation’s (NSF) Faculty Early Career Development (CAREER) Award for his research in metal additive manufacturing.
As one of the foundation’s most prestigious distinctions, the CAREER award provides grant funding to early-career faculty who have the potential to become academic leaders and role models that advance the integration of research and education.
“This award provides me with a unique opportunity to address fundamental research questions and contribute to the field of metal additive manufacturing,” Elwany said. “I feel incredibly blessed to have this opportunity to show my family and mentors how their support has been rewarded.”
Elwany’s NSF CAREER-funded research focuses on microstructure control in metal additive manufacturing and the education of the next generation of advanced manufacturing scientists and workforce in the United States.
Additive manufacturing, commonly referred to as 3D printing, is a set of disruptive manufacturing technologies that enable the fabrication of parts with high degrees of geometric complexity without the need for part-specific tooling. Elwany aims to take the technology further and produce components with location-specific properties – parts that have different properties at different locations within a single structure.
For example, a jet engine turbine has a blade with a blade root. The blade must be resistant to high temperatures and remain unchanged, while the blade root must be able to be deformed and reformed many times. Additive manufacturing can potentially be used to produce a part, like a jet engine turbine blade, with location-specific properties that cannot be found in any single material. This type of manufacturing process can also be bioinspired by structures found in nature.
“The claw of a mantis shrimp, for example, combines a hard outer surface with a tough inner core, which gives it excellent fracture resistance,” Elwany said.
He explained that these additive manufacturing capabilities will be achieved by varying local manufacturing process conditions to enable spatial control of microstructures. The ultimate goal of such research is to be able to use a single manufacturing process to create assembly-free parts with location-specific properties in the future.
Elwany’s educational objectives include plans to train and prepare advanced manufacturing scientists, engineers and workers through synergistic activities including graduate internships at Lawrence Livermore National Laboratory, study abroad programs, an outreach program for teachers and a professional certificate program.
Read more about Elwany’s research and objectives in his abstract.