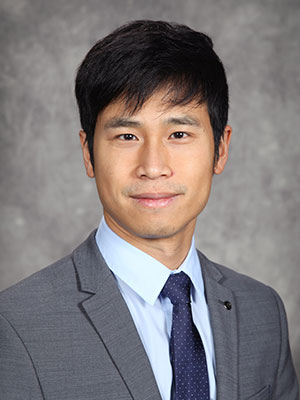
By partnering with Ford Motor Company, Dr. Bruce Tai hopes to accelerate his research into the development of a new minimum quantity lubrication machining process – an advancement that could provide such benefits as a significant reduction in water waste, energy use and costs.
Tai and his collaborators on the project, including Dr. Wayne Hung of the engineering technology and industrial distribution department at Texas A&M University, were recently awarded a new grant from the National Science Foundation that will enable the researchers to continue furthering their work in addressing this real-world problem through the Grant Opportunities for Academic Liaison with Industry funding mechanism.
Tai, an assistant professor in the J. Mike Walker ’66 Department of Mechanical Engineering at Texas A&M, said the goal of the project is to advance the current minimum quantity lubrication machining technology – that uses a small amount of oil mist in machining rather than the traditional wet process – and to address the industrial needs for machining efficiency.
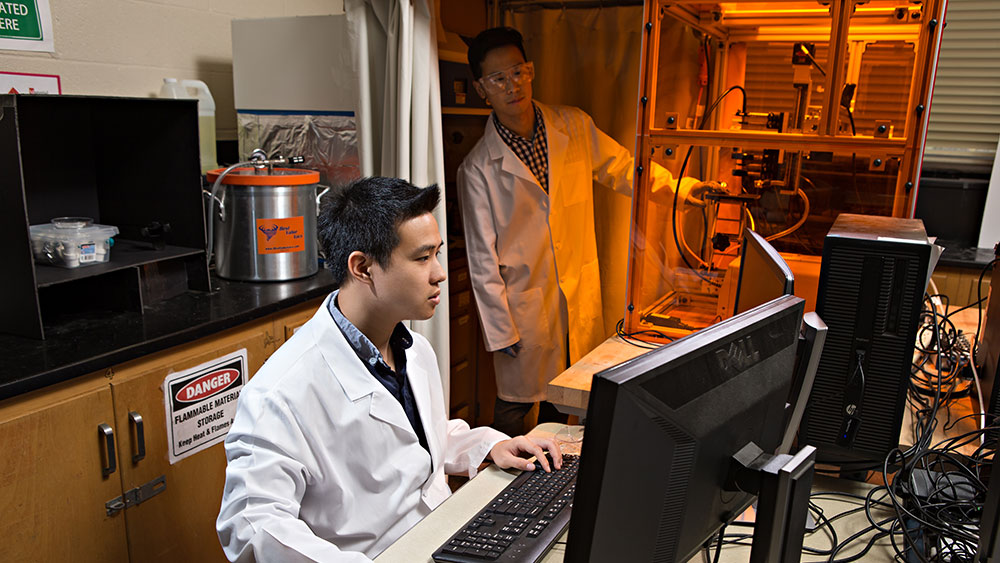
If successful, the research could lead to global benefits through new machining practices in cutting tool design, optimal machining parameters and flow systems in a broad range of areas that include the automotive, aerospace and defense industries.
With the emergence of 3D printing technology and its capabilities, Tai believes they could be used as a tool for customizing complex machining tools with internal features in the lab.
"Minimum quantity lubrication can be a challenge and risk in production when the mist flow cannot be effectively controlled to lubricate and cool down the machining spot," Tai said. "In this project, we will use 3D printing technology to customize the tool design and internal features to help us analyze flow pattern in a more systematic and parametric fashion."
Access to the full-scale, state-of-the-art facilities at Ford is also expected to provide beneficial opportunities to move the manufacturing research forward for efficiently.
Also, where typically minimum quantity lubrication machining requires a time-consuming and expensive process of extensive tests to correlate the relationships among the machining tool, flow parameters and machining performance, Tai and his group have found another approach.
"We attack this problem by looking to the black box and finding what happens mechanistically," Tai said. "This will help the industry make more accurate decisions in a more efficient way."