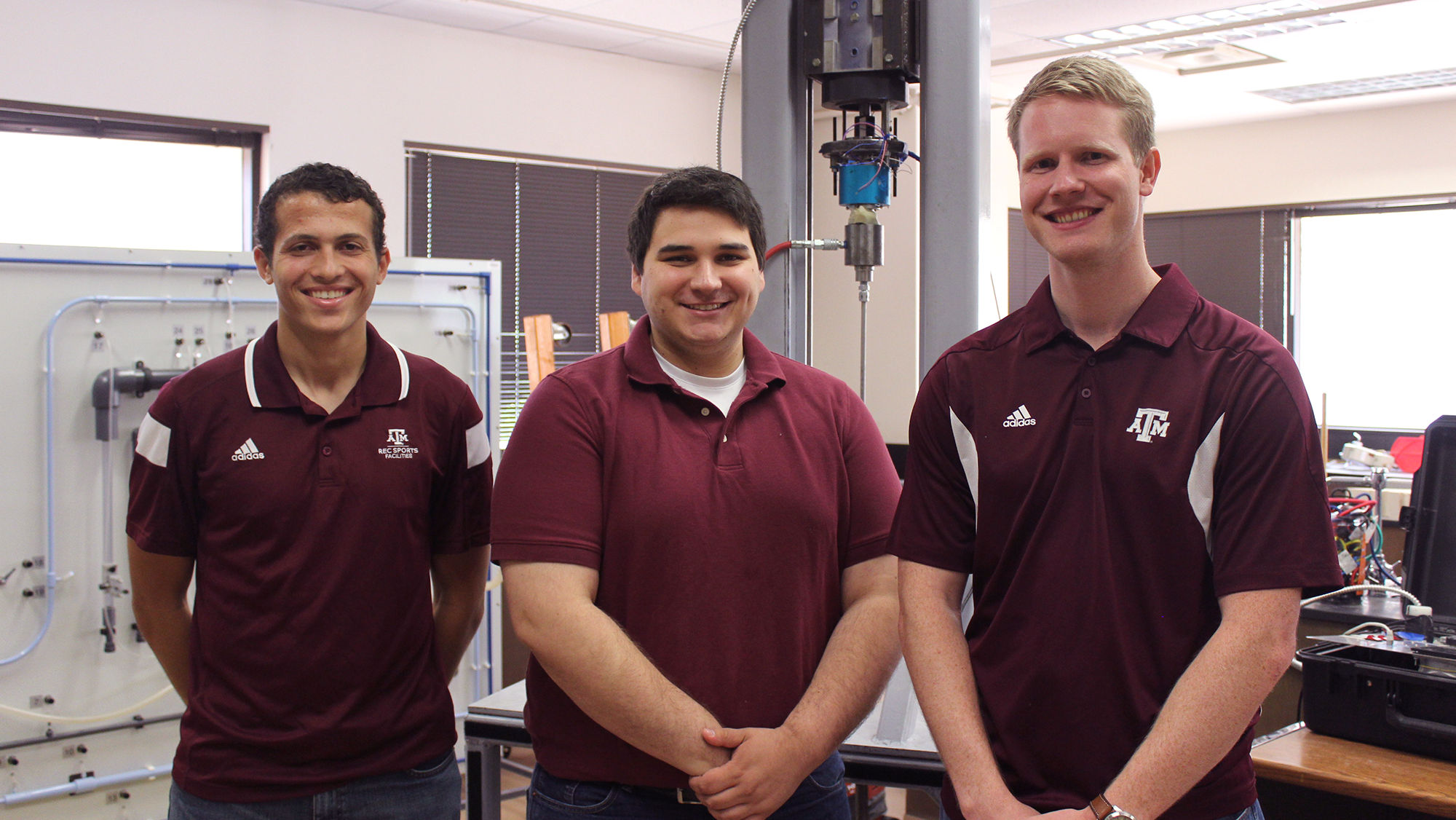
From fall 2017 to spring 2018, a record nine student teams from universities around the world built small-scale drilling rigs as part of the Society of Petroleum Engineers’ international Drillbotics competition. These rigs utilized mechanics, sensors, computer logistics and software designed by the students to drill a vertical well in a test formation of unknown composition without any human intervention. The goal is to advance the use of automated technology in drilling.
The Texas A&M University Drillbotics team placed third in the competition, which has become known for advanced logistics, innovative designs, and creative solutions as it tests the limits of what automation, and students, can accomplish. Coming in third after winning last year might be seen as a stepdown, but Texas A&M has set a precedent as the only university to place every year.
“It certainly does point to our consistency that we’re the only team who has been third or higher in every competition so far,” said Dr. Sam Noynaert, assistant professor in the Harold Vance Department of Petroleum Engineering. “That says a lot about the quality of students we have.”
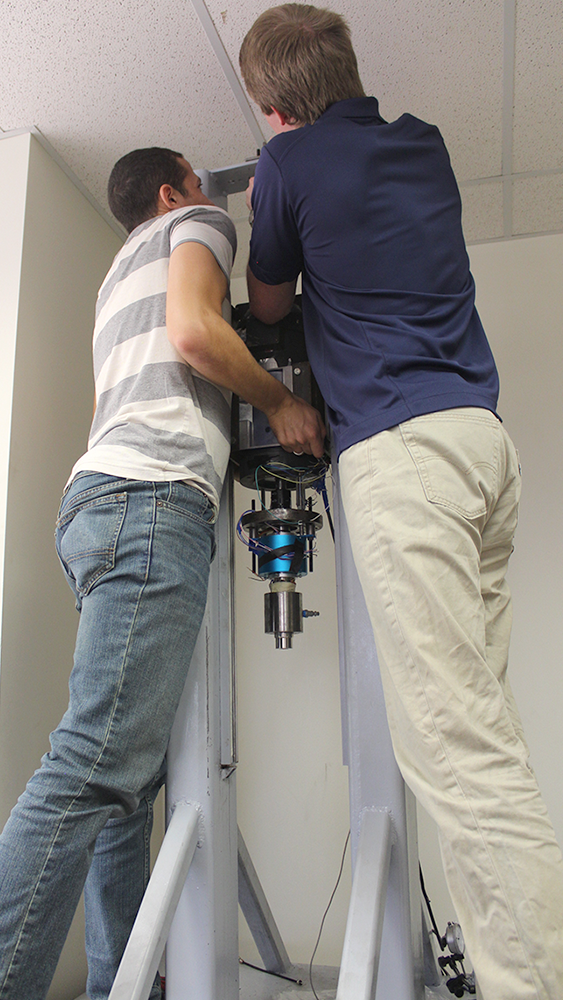
Hard work hones skills
Texas A&M enters the competition with a new team and new members every year. Some have been all petroleum engineering students and some, like this year’s team, were all from different departments. Each team can have up to five members. The only constant is the need to work together and bring all skills on board to overcome the challenges.
Petroleum engineering master’s student Ibrahim El-Sayed, mechanical engineering master’s student Nick Timmermann and electrical engineering master’s student Siddarth Biyani labored through months of preparation, design, mechanical issues, software testing and presentation writing. Undergraduate petroleum engineering student Gabriel Tatman, an unofficial but readily adopted team member, crafted the safety screens to protect onlookers while the drilling was in progress. All were quick to point out that the rewards of their hard work were higher than just winning a place.
“The scope of being able to tackle this demonstrates a lot of skills,” said El-Sayed, who was recognized by a job interviewer for his participation in last year’s competition. “It’s been immensely beneficial. There are a lot of similarities with what’s going on in the real world.”
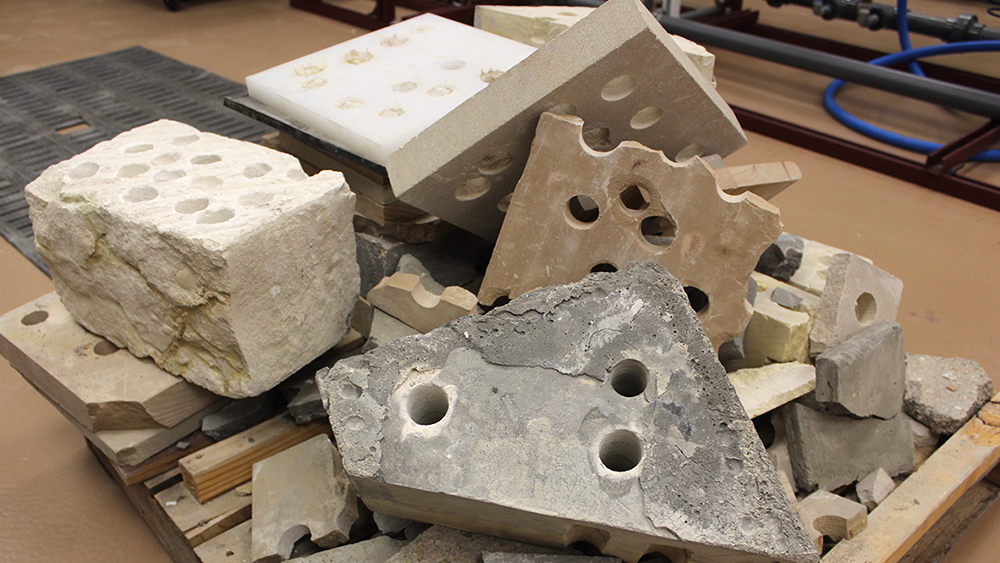
Hands-on education
Students have two semesters to meet a new set of design hurdles, technology requirements and equipment changes each time. For instance, the 2017-18 year featured larger drill pipe specifications, meaning drilling could be faster and more aggressive. The concept of plug and play was also introduced, where teams had the option to take their rig’s software and plug it into another rig to test functionality. This functionality test will be mandatory for 2018-19.
Some of the more innovative designs from all the teams in the 2017-18 contest included:
- Design and construction of a non-aggressive polycrystalline diamond bit
- Improved pipe couplings
- Hammer assisted drilling
- Novel bottom hole assembly designs and 3D printed sensor subs
- Several new telemetry techniques from the downhole sensor
- Optimization algorithms
- Dual control loops not affected by the loss of a single sensor
- Auto-generated drilling reports
As with any project, being a part of the Drillbotics team can be exciting, daunting, frustrating and immensely satisfying, but the students maintain it is an excellent addition to their education.
Timmermann, who received his bachelor’s degree in petroleum, commented, “I took Mr. Dupriest’s class (in spring 2017), the high-performance drilling class, and it’s been really cool to see this, what he talked about in his class, right in front of me.”
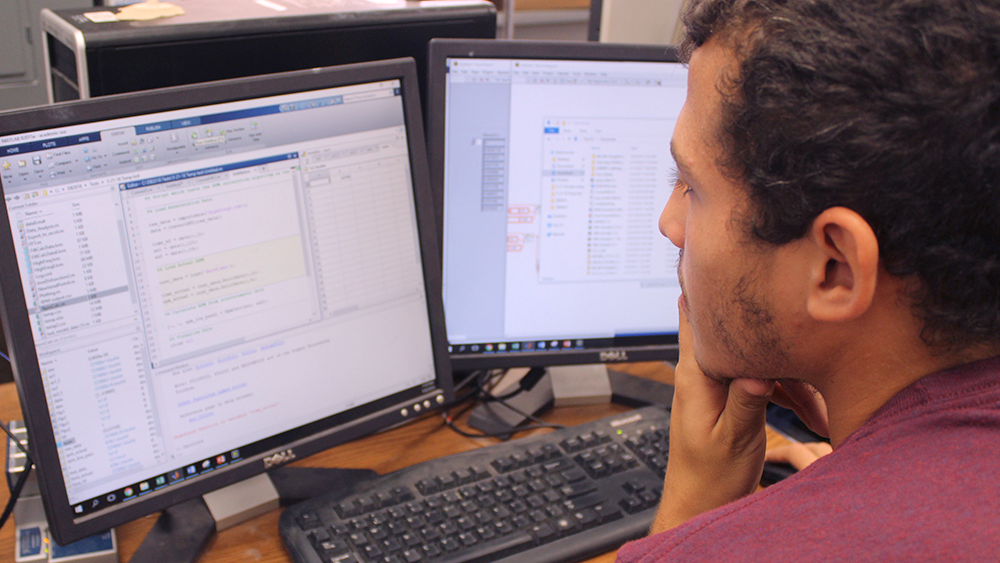
Paper and patent
Teams build on the work done the year before, as much as possible, and the results have been impressive. The winning team last year wrote and submitted a paper at the Society of Petroleum Engineers’ International Association of Drilling Contractor’s drilling conference and exhibition in Fort Worth titled “Lab-Scale Drilling Rig Autonomously Mitigates Downhole Dysfunctions and Geohazards Through Bit Design, Control System and Machine Learning,” by E. Zarate-Losoya, T. Cunningham, I. El-Sayed, S.F. Noynaert and F. Florence. A patent was also submitted for technology the students designed.
“The patent is on the control systems,” explained El-Sayed. “It’s about using a control system to identify the drilling set points with the assistance of a machine-loading model that predicts where to drill.”
History and future team
The Drillbotics competitions originated when several Society of Petroleum Engineering members saw the need to increase the use of automation in the drilling industry. They established the Drilling Systems Automation Technical Section and thought student competitions were the perfect way to introduce the topic. Four years later, Drillbotics has grown dramatically, both in scale and scope, leading to a friendly international rivalry among the students to come up with the most innovative systems possible.
“We’ll be putting together the new team in the fall,” said Noynaert, who named petroleum engineering master’s student Cameron Gerasti as the 2018-19 team leader. “This is the hardest part – having to rebuild a team every year - which also speaks to the overall quality of students at Texas A&M that we can do this repeatedly with different students each year and still have success.”