- Associate Professor, Mechanical Engineering
- Gulf Oil/Thomas A. Dietz Career Development Professor
- Phone: 979-458-9888
- FAX: 979-845-3081
- Email: btai@tamu.edu
- Office: MEOB 413
- Website: Research Webpage
- Linkedin: Profile
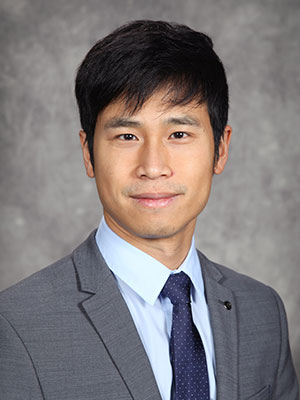
Educational Background
- Ph.D., Mechanical Engineering, University of Michigan, Ann Arbor – 2011
- M.S., Applied Mechanics, National Taiwan University – 2006
- B.S., Civil Engineering, National Taiwan University – 2004
Research Interests
-
- Non-traditional machining processes
- Numerical modeling of manufacturing processes
- AI in manufacturing
- Additive and hybrid manufacturing
- Surgical simulation and data analytics
Awards & Honors
- ASME Fellow - 2022
- TEES Engineering Genesis Award - 2019
- TEES Young Faculty Fellow Award, Texas A&M University - 2018
- Outstanding Young Manufacturing Engineer Award, Society of Manufacturing Engineers (SME) - 2017
- Blackall Machine Tool and Gage Award, American Society of Mechanical Engineers (ASME) - 2017
Selected Publications
- Nigam, A., and Tai, B. L., 2024, "Effects of in-process surface finishing on part strength in polymer material extrusion additive manufacturing," Additive Manufacturing, 80, p. 103960.
- Raval, J. K., and Tai, B. L., 2022, "Mist Flow in Through-Tool Minimum Quantity Lubrication Drilling: Two-Phase Flow Simulation and Experimental Observation," Journal of Manufacturing Science and Engineering, 145(3).
- Kung, P.-C., Heydari, M., Tai, B. L., et. al., 2023, "A neural network framework for immediate temperature prediction of surgical hand-held drilling," Computer Methods and Programs in Biomedicine, 235, p. 107524.
- Randolph, O., Zvanut, R., and Tai, B. L., 2024, "Microstructure analysis and machinability of additively manufactured A205 aluminum with heat treatments," Journal of Manufacturing Processes, 127, pp. 51-61.
- Nigam, A., Kellam, J. F., Tai, B. L., et. al., 2024, "A Data-Driven Methodology to Comprehensively Assess Bone Drilling Using Radar Plots," JBJS Open Access, 9(1).