Explore Texas A&M University materials science and engineering senior capstone projects completed from fall 2021 to spring 2022.
Projects
Project 1
A Method for Microstructure-Based Evaluation of Advanced High-Strength Steels
Team members: Ashley Person, Jay Wale, Kennon Wishert, Kira Oberhelman (lead)Synopsis: Strength and formability are the two important parameters for successfully implementing new steels for automotive applications. Steels with tensile strengths of 1 GPa and above are usually targeted for such applications, but similar strength levels can be achieved from a variety of steel compositions, processing conditions and microstructures. Thus, standard tensile tests are not enough to assess failure and formability of these high-strength steels and these need to be supplemented with hole expansion and bending tests. Nevertheless, these test results do not directly correlate, and the selection of suitable steel for a specific application remains somewhat arbitrary. The goal of this project is to develop a microstructure-based criterion for the evaluation and selection of advanced high-strength steels for automotive applications.
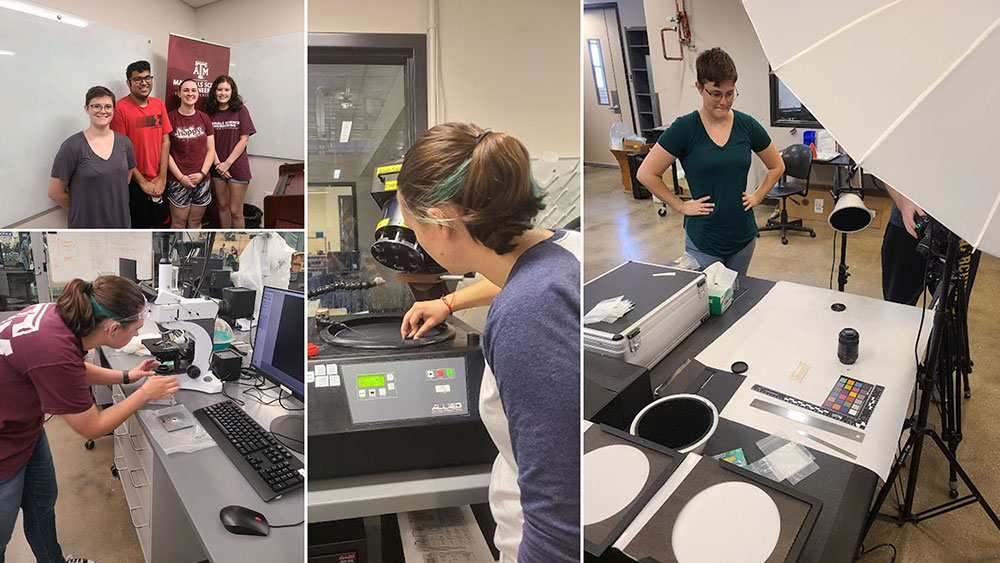
Project 2
Develop a Measurement Apparatus and Standard Method for Characterizing Dynamically Tunable Thermal Energy Storage Materials
Team members: Andrew Mirea, Benjamin Pitblado, Kaleigh Curtis (Lead), Khamila Quevedo
Synopsis: Thermal energy storage materials are critical materials for preventing electro-mechanical systems from overheating, and for storing and reusing heat to improve use of energy in buildings, displace demand on the electric grid, and storage of industrial process heat for later use. The key to further adoption of these technologies is the development of materials which respond to some external stimulus (strain, pressure, magnetic field, etc.) to tune the temperature at which they store and discharge heat. The goals of this project are to develop an apparatus and standard method to measure the quantity of thermal energy that a material can store/discharge, the response of a material to an external stress to change the temperature at which heat is stored, and the rate at which a material responds to an applied external stress.
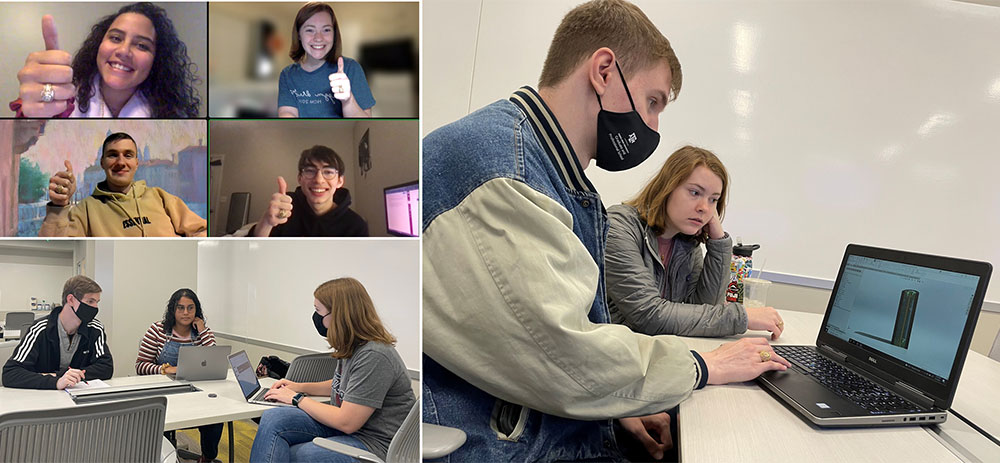
Project 3
Modeling Guided Discovery and Evaluation of New Ultra-High Temperature Ceramics
Team members: Kenna Ashen, Nicholas Williams, Tyler Shiery, Victor Vogt (Lead)
Synopsis: Hypersonic applications call for materials that can mechanically and thermally withstand temperatures above 2000 degree Celsius. Such extreme temperatures require materials with high temperature stiffness as well as resistance to oxidation due to large thermal gradients and bow shock. Our project involves the use of a machine learning model based on quantum mechanical modeling and material datasets to evaluate candidate materials and select promising compositions for experimental evaluation. Our unique modeling and computing resources will enable rapid discovery of new high-performing materials while saving significant time and costs compared to traditional experimentation and high-throughput modeling-based evaluation of materials.
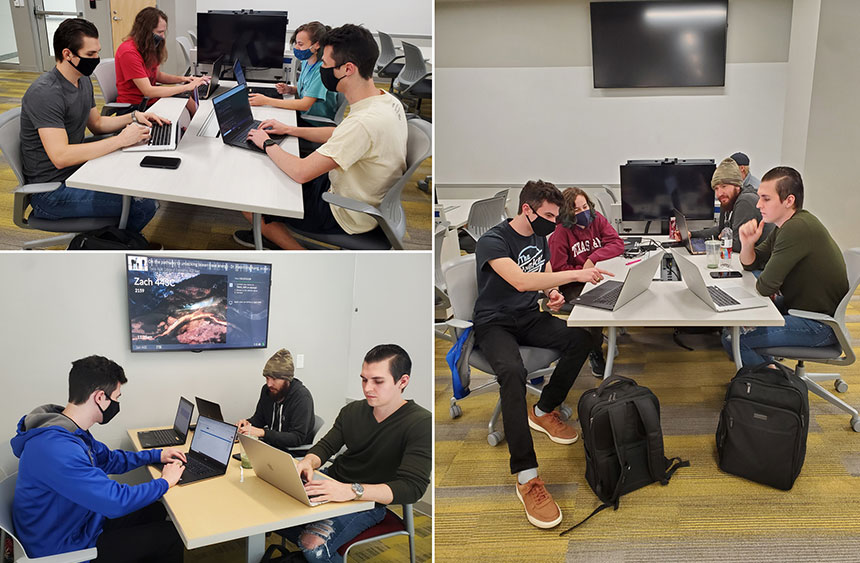
Project 4
Heat Treatment Optimization of Cold-Sprayed Additively Manufactured High Temperature Materials
Team members: Bradley Robinson, Charles Ribardo, Ion Powell, Khanh Van Pham (Lead), Zachary Nolan
Synopsis: Cold spray additive manufacturing can be used to coat materials with refractory metals, improving performance at high temperatures. In this application, helium is used a medium to cold spray niobium due to its high heat transfer coefficient, thermal conductivity and higher sonic velocity than nitrogen. The cold spray process introduces residual stress in niobium that makes it harder and reduces the ductility thus post treatments are necessary to improve the performance. This project is focused on improving niobium’s material properties, primarily the toughness. The final goal of the project is to define an optimal post-treatment process for cold-sprayed niobium through a series of mechanical and microstructural characterization methods, that will yield improved mechanical properties such as toughness and ductility.
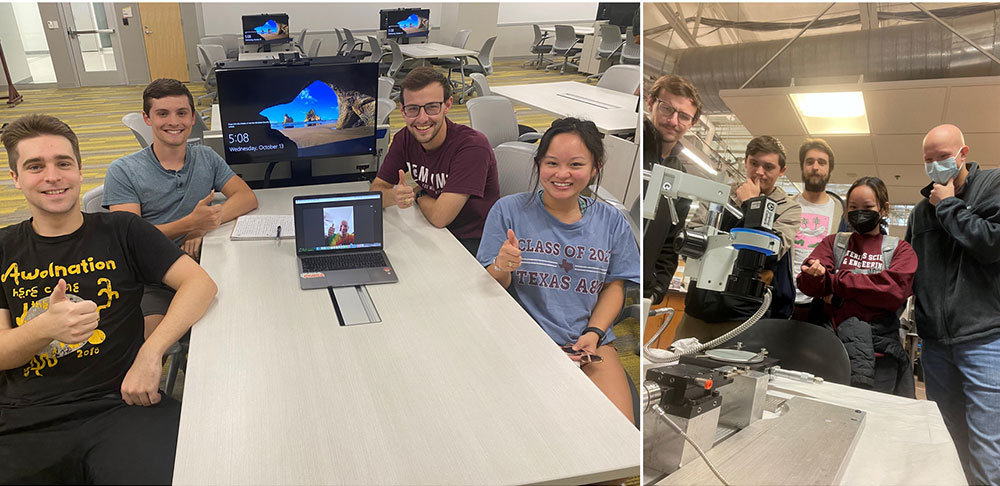
Project 5
Mitigating Corrosion and Degradation of Metallic Fixtures Used in the Galvanizing Process
Team Members: Bethel Oluwole, Charles Shoalmire (Lead), Peyton Usoff, Ritai Su
Synopsis: During the hot dip galvanization process, the steel fixtures used to secure metal parts experience mechanical degradation as they repeatedly go through the process, leading to increased risk to workers and increased cost for replacing the fixtures. These steel fixtures experience highly caustic and acidic solutions, and temperature exceeding 450 degree Celsius. This project seeks to develop a nickel-based coating for the fixtures that can increase their lifespan by reducing corrosion that occurs during the pickling process. Our solution, if implemented, will increase fixture lifespan, increasing safety for workers and reducing replacement cost.
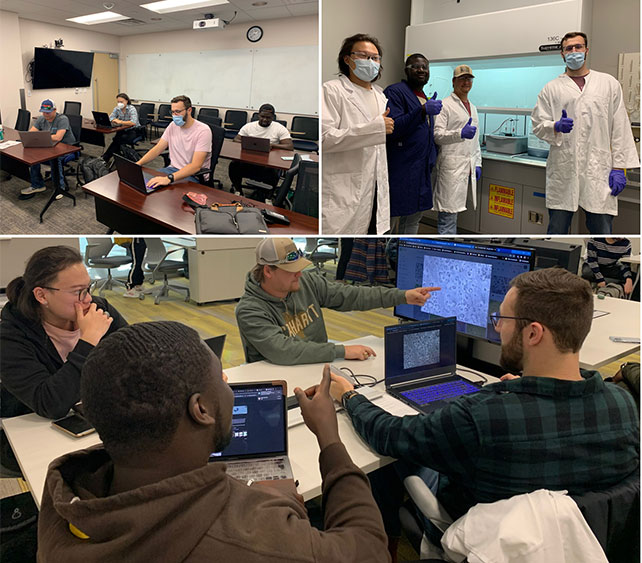
Project 6
Test Apparatus and Methods for Testing Multifunctional Devices and Materials
Team members: Andrew Worthy, Brian Carpman, Gabrielle Garza (lead), Vanessa Trevino
Synopsis: During manufacturing of commercial airliners in large subassemblies, unwanted gaps may form when parts are brought together. Shims made of shape memory alloys (SMA) can solve this problem by expanding inside the gap upon the application of heat. This project focuses on designing and building an apparatus that can thermo-mechanically test these SMA shims. A major challenge is to test the unique shapes of the shims while accurately measuring and controlling the force, displacement, and temperature, as well as measuring shape change. Shims of different shapes and compositions will be tested and the collected data will be analyzed to determine the suitability of shim designs for different cases.
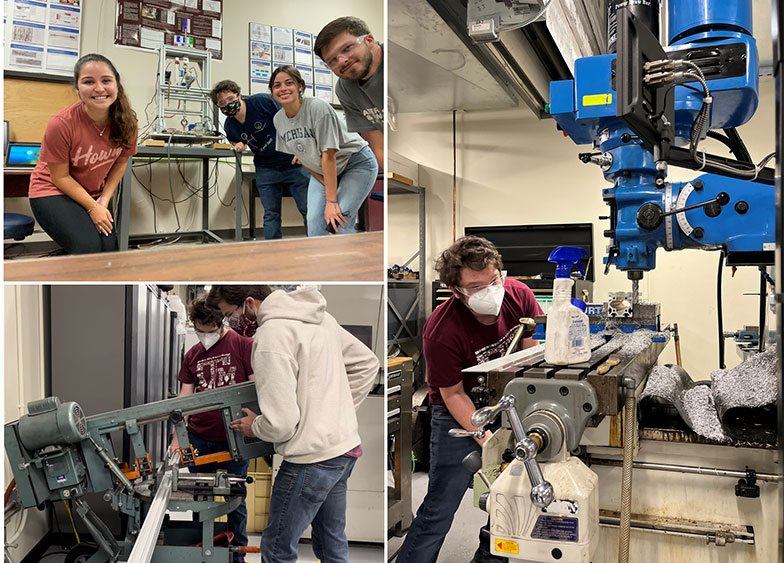
Project 7
Design, Additive Manufacturing, and Testing of Nickel based Superalloy Components
Team members: Adam Light, Andrew Thomas, Esteban Nava Sanudo, Joseph Messmer (Lead), Reid Harrison
Synopsis: 3D printing has revolutionized manufacturing and has also become an insurance policy against costly supply chain interruptions. Our project involves laser powder bed fusion (LPBF) of Ni-based superalloy valve trims as an alternative method to conventional machining and investment casting processes. Some of the challenges associated with 3D printing of intricate Ni-based superalloy parts is the achievement of a defect-free structure and meeting of dimensional tolerances. Successful completion of this project will enable cutting out long wait times caused by shipping delays, and instead produce ready-to-use parts on or near the site for valve manufacturers.
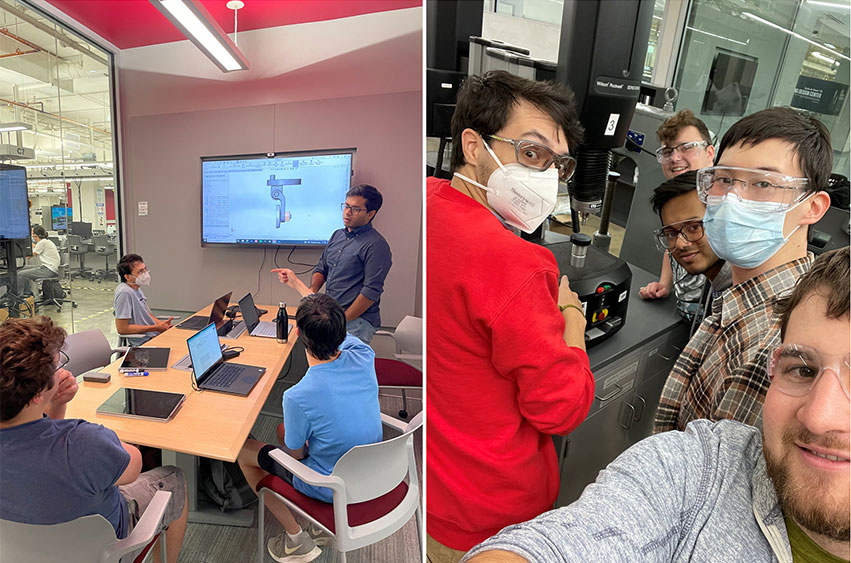
Project 8
Experimental Design for Testing Elastomers in High Pressure supercritical carbon dioxide
Team members: Benjamin Barkai (lead), Carolina Martinez, Minzhang Qiu, Oliver Martinez Defillo
Synopsis: Supercritical carbon dioxide has many industrial uses such as oil extraction and carbon transport. However, supercritical carbon dioxide is soluble in pipeline elastomer O-rings, and in the case of a rapid decompression, the dissolved fluid will expand, leading to blistering, tearing and cracking of the O-rings. A leak in pipeline contents can then lead to environmental harm, economic damages, and injuries. Our project seeks to design an autoclave setup that would rapidly decompress different O-ring materials exposed to different grades of supercritical carbon dioxide. O-ring materials can be inspected for failure afterward, which can show if the selected material is suitable for the pipeline, reducing risks in the industry.
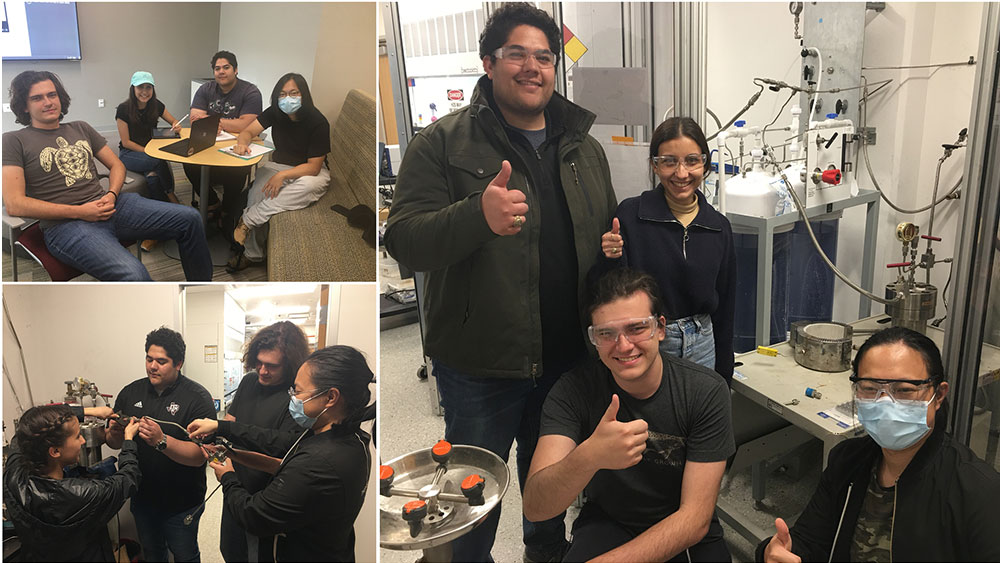
Project 9
Instrumented Tool Holder for Quick Indication of Machining Performance
Team members: Aaron George (lead), Claire Swank, David Skillern, Joseph Duran
Synopsis: Improper machining practices used by inexperienced machinists result in excessive manufacturing costs. In this project, an instrumented tool holder with strain gauges and electret accelerometers is designed that measures and analyzes force and vibration data, then displays an indication of performance to the machine operator, thus decreasing the machining experience needed to operate a milling machine successfully. Our project would benefit machinists by providing them with a tool that can decrease the time and money spent while machining and improve the training process.
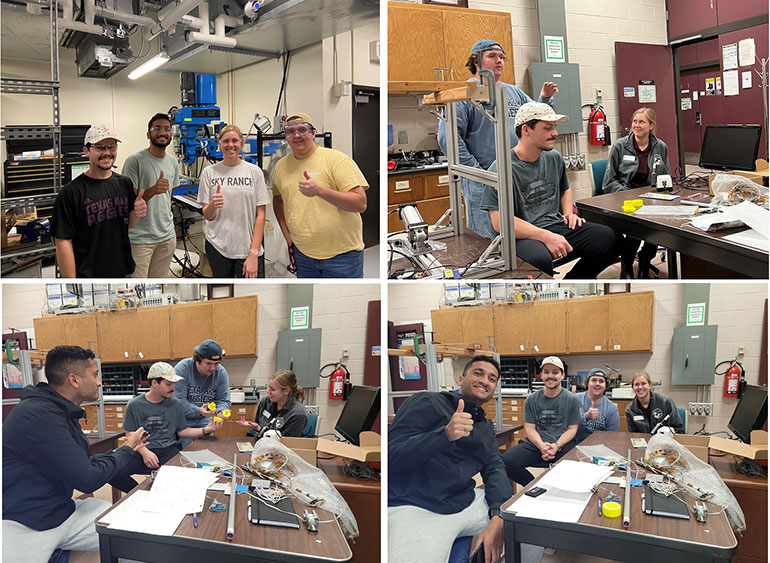
Project 10
Modular Mannequin Leak Test Development
Team members: Gualberto De La Garza, Kaydia Thomas (involved only in fall 2021), Nhu Vu, William Bryan (lead)
Synopsis: The objective of this project is to create modular mannequins that can change size, weight and position to test hygiene products for young children and senior citizens. Current diaper and adult incontinence testing methods fail to consider weight variations for both age groups and require a unique mannequin for each product size. These test mannequins cannot change positions individually and leave many sizes untested. Replacing the existing testing model with a modular one readily changes the significant variables, widens the range of test products, increases testing speeds, and decreases the upfront testing costs.
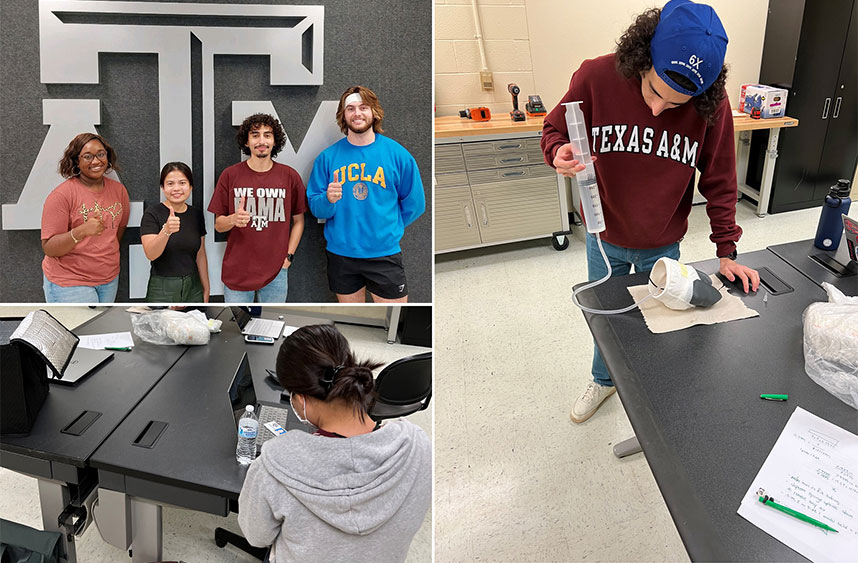
Project 11
Developing a Protocol for the use of Carbon dioxide Corrosion Model for Failure Prediction
Team members: Curtis Le, Hadyn Kroen, Jessica Elder (lead), Samuel Mendoza
Synopsis: Extensive and uncontrolled corrosion can lead to system failures in multiple industries. Many models are developed to simulate corrosion mechanisms. However, there is a difference between the predictions of all models and actual field failures. Thus, we compared the accuracy of multiple standard models in predicting corrosion rates of low alloy carbon steels in carbon dioxide aqueous environment. Finally, the goal is to quantify the deviations between the predictions of the models and measurements in an effort to improve modeling techniques to better manage corrosion and avoid catastrophic field failures. A protocol and recommendation on what models to use will then be recommended.
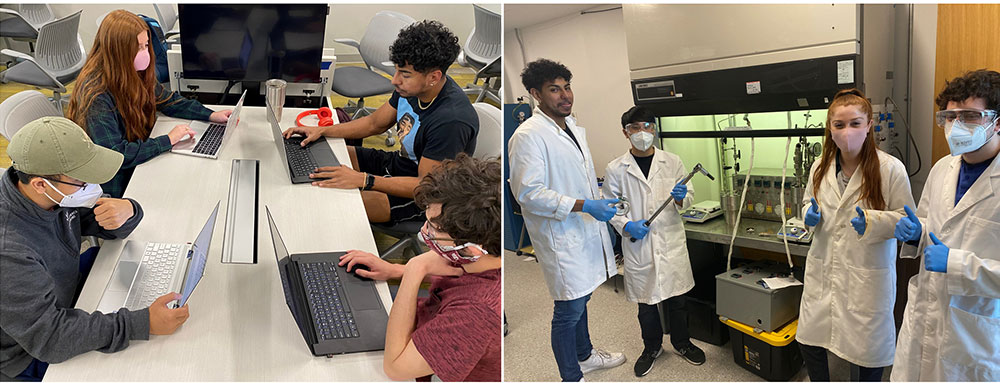
Project 12
Designing a Microstructure to Improve Super-elasticity in Nitinol
Team members: Chinwe Akuechiama (lead), Diego Macias, Grant Pearson, Hannah Limburg, Peter Evans
Synopsis: Medical devices, such as stents, must reliably perform intended tasks for long periods of time. Commercial Nitinol is an alloy popularly used in medical stents owing to its unusual superelastic response to stress. Biomedical companies are developing alternate Nitinol compositions with different thermal historiesin an effortto improve the superelasticity levels of the commercial Nitinol. By comparing commercially available Nitinol to NitinolX, a new Nitinol composition with unknown properties, we have chosen and proposed an ideal microstructure for this new alloy to increase its superelasticity. This improved material should offer maximized efficiency, enabling improvements and innovation that are not possible with limitations of commercial Nitinol.
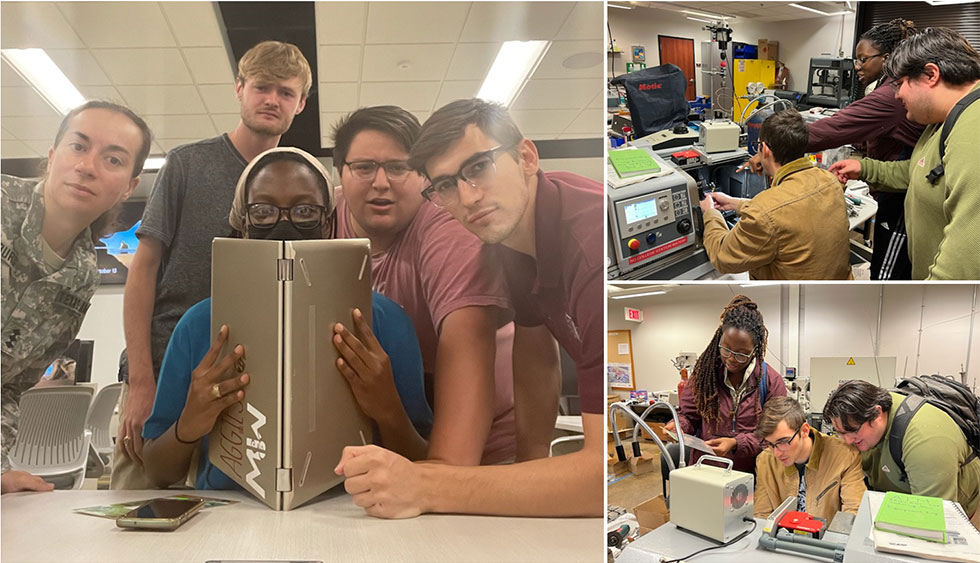
Contact
For information about fall 2021-spring 2022 projects, contact:
Ankit Srivastava
Associate professor, materials science and engineering
Email: ankit.sri@tamu.edu
Kadri Can Atli
Instructional associate professor
Email: catli@tamu.edu