The Aggie Drilling Research Group (ADR), headed by Dr. Jerome Schubert, has recently completed the construction of a new dual gradient drilling lab located in the University Services Building. The equipment is currently set up to model a deepwater dual gradient riser/subsea pump/return line system utilized in ultra-deepwater drilling. The deepwater drilling industry has been developing dual gradient drilling technology to mitigate many of the drilling problems that are common while drilling in water depths greater than 6,000 feet.
Schubert (shown left) is an associate professor in the Harold Vance Department of Petroleum Engineering and has specialized in this research for many years. He was involved with a groundbreaking 1995 dual gradient drilling study at Texas A&M University and has several patents related to this process.
“The problems are due to the need to maintain the pressures in the well within a very narrow pressure margin,” Schubert said. “Dual gradient drilling is designed to widen this pressure margin and to manage the pressure profile in the well within close tolerances.”
The pressure gradient in land drilling begins at the top of the well where the pressure is equal to one atmosphere (the weight of the air on the Earth’s surface) and rises as the drill bit travels down through the wellbore (and the rock surrounding it) to reach the bottom of the well, which is sometimes thousands of feet below the surface. Heavy mud is circulated down the drill string and back up through the annulus area of the well to counter the high pressure at the bottom and prevent it from forcing the oil into the wellbore. Continued circulation is done to remove the drilled cuttings.
The pressure gradient begins at the surface of the water when drilling in the ocean, but the area between the surface of the water where the rig is and the seafloor where the well actually begins adds complications. The wellhead and blowout preventers are located at the seafloor and connected to the rig by the drilling riser. Since the riser is surrounded by water, it is under different pressures. Dual gradient drilling solves this by adjusting the interior riser pressure, usually with seawater (or a fluid of the same density), and then fills the well with the density of mud needed to give the proper balance just like in land drilling. These pressures are regulated and maintained by special pumps, blowout preventers, and many checks and balances.
Special difficulties are presented while drilling in ultra-deepwater. BP encountered some of these while drilling the Macondo well prior to the 2010 blowout, which led to some of the decisions BP made that were highly criticized. As with all new technology, there are phenomena that are not fully understood.
“Our lab is designed to help the industry better understand what will happen in the junction between the marine drilling riser and the subsea pump,” said Schubert, who served as an expert adviser on the Macondo situation aftermath.
The current work studies the behavior of natural gas entering the riser, one of the difficulties BP had to deal with. The source of the gas can be from the formation that is drilled up and circulated to the surface. Due to pressures in the formation, gas contained in the pore spaces of the rock that is drilled up will expand as it is brought toward the surface. This lab should help visualize the path this gas takes.
“We hope to determine how much gas entering the riser is diverted to the subsea pump and how much continues upward and accumulates at the top of the riser, and how we can maximize the gas that exits through the subsea pump,” Schubert said.
Gas can also enter the wellbore from kicks. A kick occurs when formation fluids flow into the wellbore due to insufficient pressure being maintained within the wellbore. Kicks have to be handled differently than drilled gas, since these can escalate into a blowout. Currently gas from kicks is kept out of the riser by closing the blowout preventers and circulating it to the surface via a small diameter choke line. A high pressure choke at the surface is adjusted to impose back pressure to the well so that the kick can be killed properly. Newer risers are being designed with gas handling equipment installed in the top of the riser.
Part of this study will develop procedures where the riser itself can be utilized in handling this gas from kicks. This type of research will help future drilling operations recognize and avoid the dangerous pressure situations that led to the Macondo blowout, and possibly create safer equipment to further reduce risk.
The lab system consists of clear PVC pipe (six inches in diameter) to simulate the marine drilling riser, small diameter clear PVC inner pipe to simulate the drillstring and a six-inch outlet approximately six feet from the bottom of the “marine riser” to act as the outlet of the riser (inlet of the subsea pump). There are two centrifugal pumps: one to act as the mud pump where they can pump straight up from the bottom of the riser or down the drillpipe and up the riser annulus, and one connected to the riser outlet to act as the subsea pump (either for the enhanced drilling EC Drill pump or the SMD Mudlift pump). Finally there is an air compressor used to pump air into the bottom of the riser to simulate gas entering the system. The clear pipe is mounted to a steel frame which can be lifted from horizontal to vertical by a winch attached to a beam in the building. The lab can run experiments at any angle from horizontal to vertical. Videos from the experiments can be viewed here.
The steel frame was constructed from funds provided by the Bureau of Safety and Environmental Enforcement (formerly the Minerals Management Service) for a project Schubert and his students conducted to study if epoxy-like materials could be pumped into a well near the surface and drop up to 7,000 feet in an annulus, accumulate on top of a packer, and set in a vertical and deviated well. Funding for the current piping, pumps and instrumentation has been provided through the Marilyn and W. F. Albers ’47 Faculty Fellowship, and funds received from directional drilling short courses conducted by Halliburton for their employees using the petroleum department’s drilling simulator. The current configuration was constructed predominately by Omer Kaldirim, a master’s student in petroleum engineering (shown in second picture), and John Maldonado, the facilities manager for the department of petroleum engineering. Aaron Mendonsa, another graduate student, also works on this project.
For more information on the lab and research, please contact Jerome Schubert. (jschubert@tamu.edu)
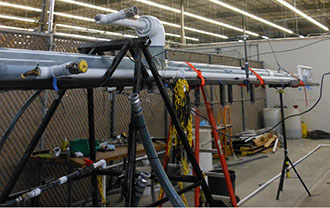